In sunny Breisgau, Germany, in-akustik has been manufacturing cables for more than 46 years and incorporates German engineering craftsmanship and great vertical integration into its products in the best sense of the term. This may sound like somewhat dusty marketing-speak, but in practice turns out to be extremely exciting.
Why do we routinely visit manufacturers and distributors? On the one hand, of course, it’s nice to get out in the fresh air and meet people. But above all, it sharpens our senses for the experience, skill and expertise of the companies we visit. Of course, we can take a much closer look at products in our own listening room. But we concentrate primarily on the sound and feel as well as two or three core features of the test object. All the little details, the meticulousness of the employees and the sophistication with which they ensure that one product succeeds as well as another, remain hidden behind a veil. Let’s take in-akustik as an example – because I just happened to be there.
Based in rural Ballrechten-Dottingen (find it on a map a bit south of Freiburg), a “border crosser” between cable manufacture and distribution, I’ve never really been able to categorize the company. Founded in 1977 by Günther Sumser as a pure production facility for signal conductors, the Breisgau-based company (Breisgau is the name of the region where Ballrechten-Dottingen is located) is among the well-established names of the German HiFi landscape. In 1980, their own label was added, followed by the associated media distribution in 1985. Parallel to this, in-akustik is of course also an importer and distributor for products from Primare, Audiovector, Koss, Stoic and AmbienTech. A real jack of all trades. Of course, it was clear to me that the company’s own house brand, the cables under the “inakustik” label, play a predominant role. But how much of the company’s resources go into its own products and at what level the production takes place, I realized only during my visit in February.
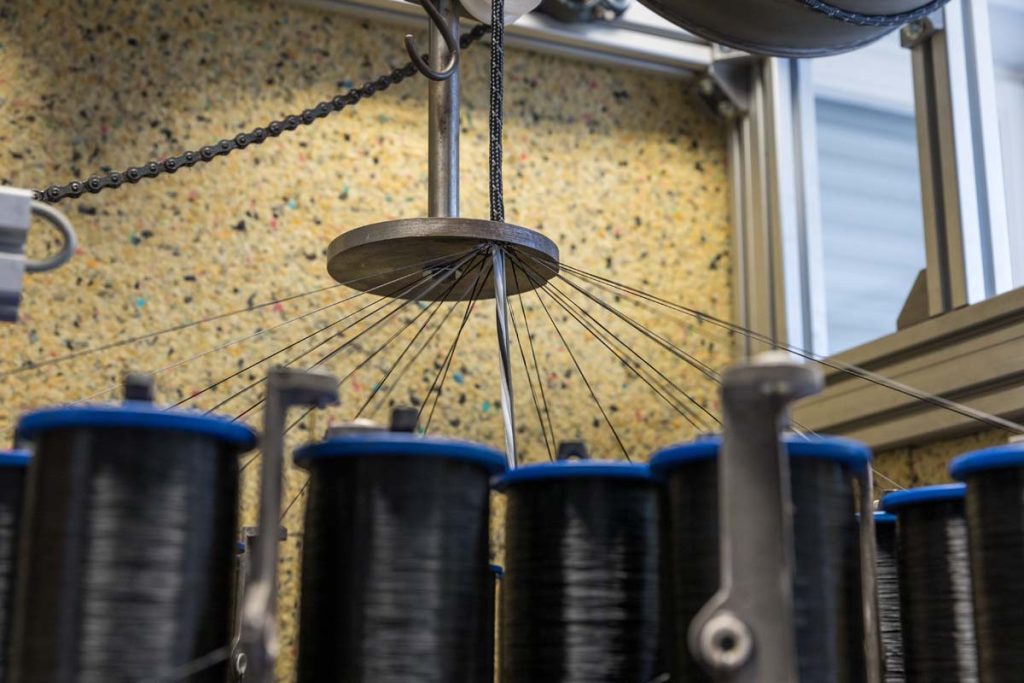
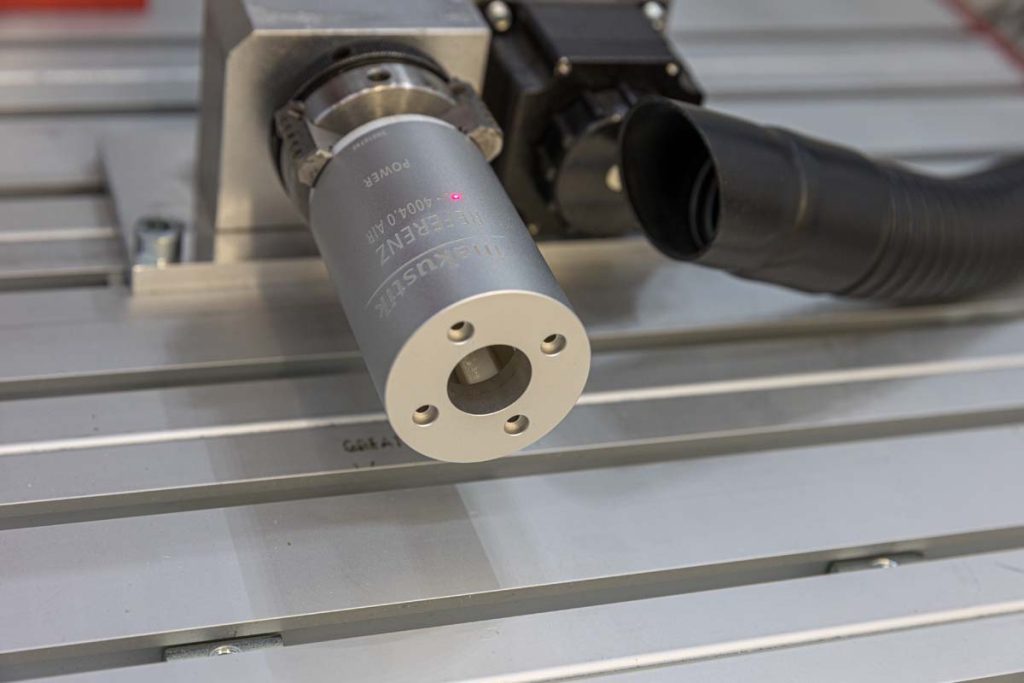
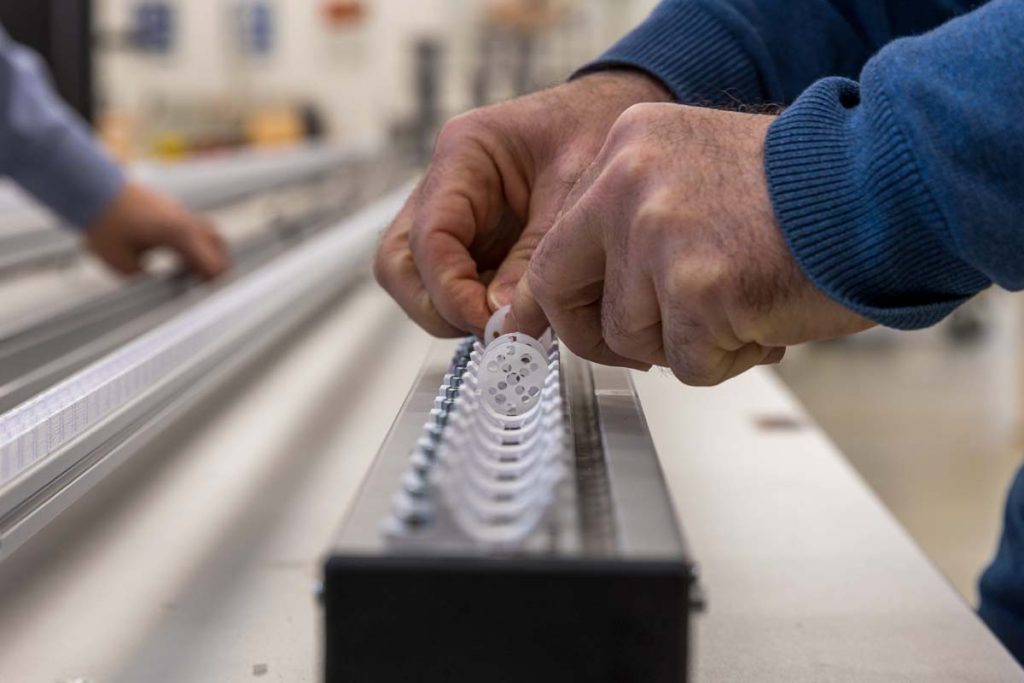
I was welcomed by a good-humored trio: Managing Director Dieter Amann, developer Holger Wachsmann and Marketing Manager Tobias Tritschler led me into a conference room with a view of the greenery. After our greeting, I immediately wanted to get a question off my chest that had been bothering me the most during the trip: Why was the cable portfolio of Black & White changed to “inakustik” in 2006? I could tell from Dieter Amann’s prompt answer that this was not the first time he had heard this. Cable production was originally launched as “inakustik”. When the company went on sale in 1998 with a new reference series in striking black and white, it was considered a given that the premium models would stand out with their own brand. But as it happens, in order to profit from the good reputation of the super cables, “Black & White” was transferred to ever cheaper lines until no one really knew where the boundaries were. The hard cut ensured order. And hey, the cables themselves are still black & white …
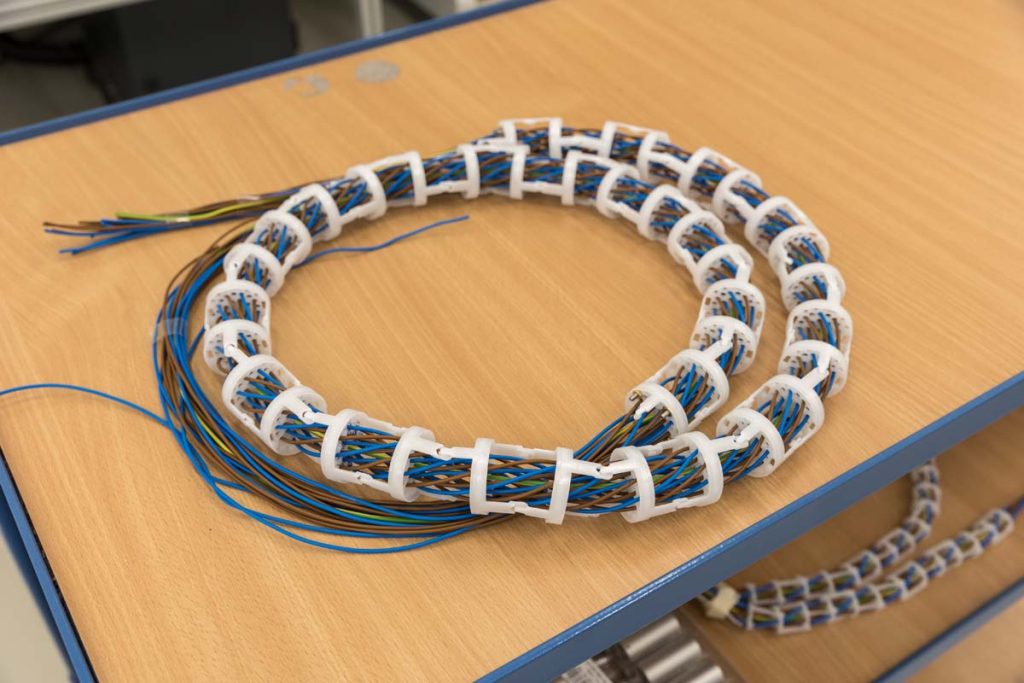
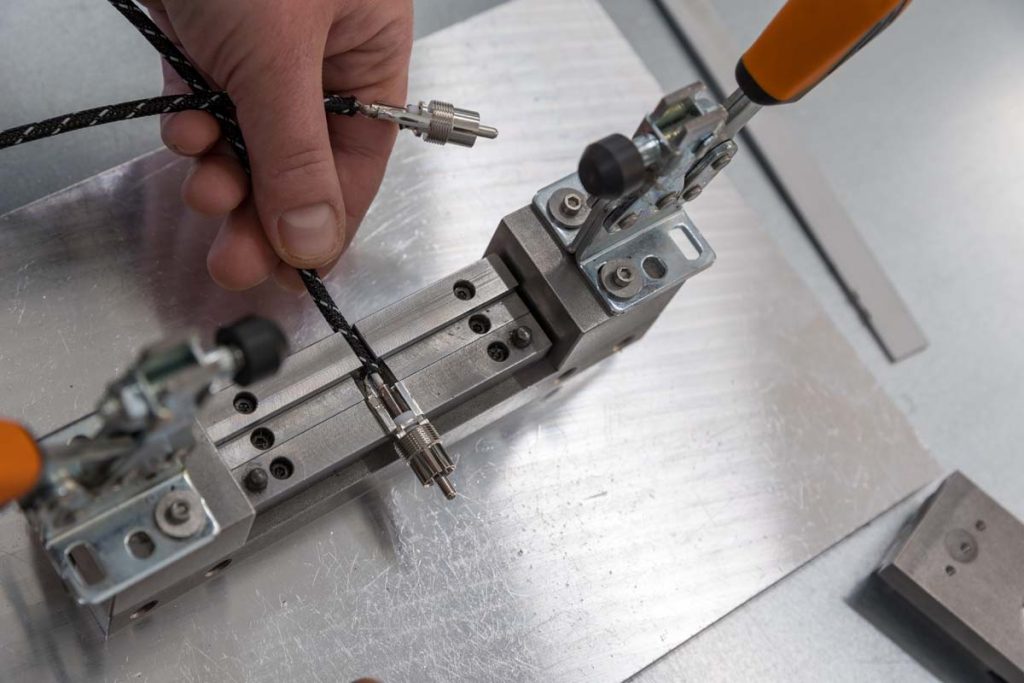
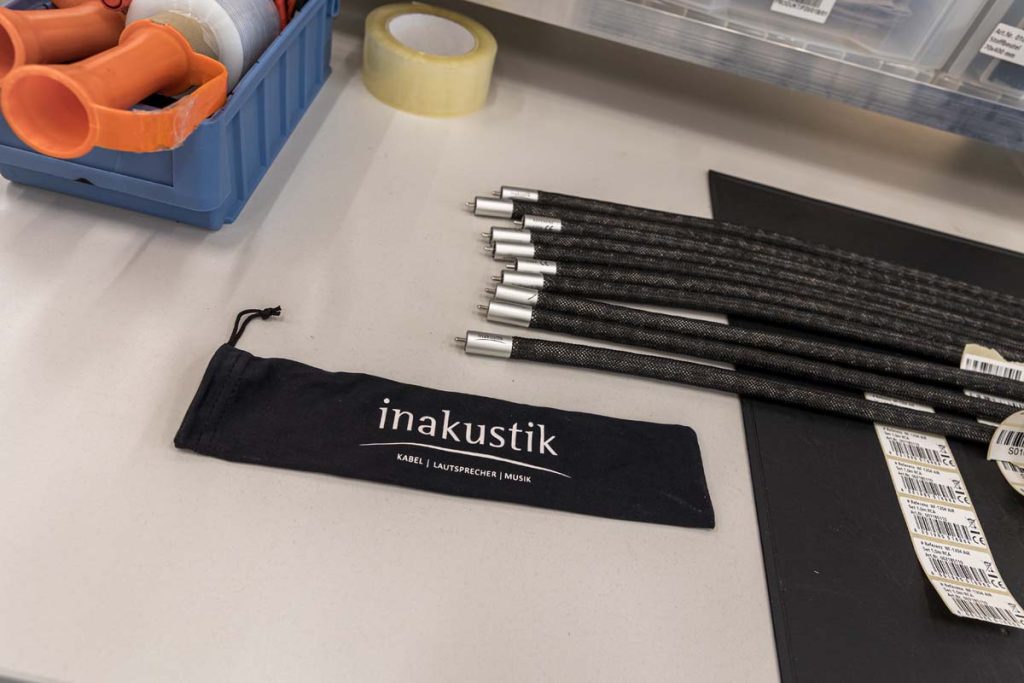
Rather than talk and talk, we decide to head directly to the large production hall right away. In the clearly structured hall, a handful of employees are busy carrying out various work steps at six elongated workbenches. The individual stations are optimized for specific production stages, as Holger Wachsmann explains to me. The employees complete a kind of circuit training with the cables they are currently assembling, finding all the tools and accessories required for the work step at the tables. This arrangement ensures synergies: The smaller models pass through the same hands, benefit from rehearsed precision, and are cut, soldered, or screwed together with the identical machines as the precious AIR models.
Holger Wachsmann and Dieter Amann demonstrate some of their “apparati” to me. There is a small wire stripper, for example, a machine that at first glance seems inconspicuous and could also be found in a medical laboratory. The small box is programmed with all the cable types used and cuts off the predefined part of the conductor sheath with millimeter precision. Just one table away, an employee is busy finishing some reference AIR power cables. She uses a torque screwdriver to screw together the carbon enhanced Schuko plugs. Each type of plug has its own requirements, I learn. On the shelf above the workbench are several of the screwdrivers with different Newton ratings.
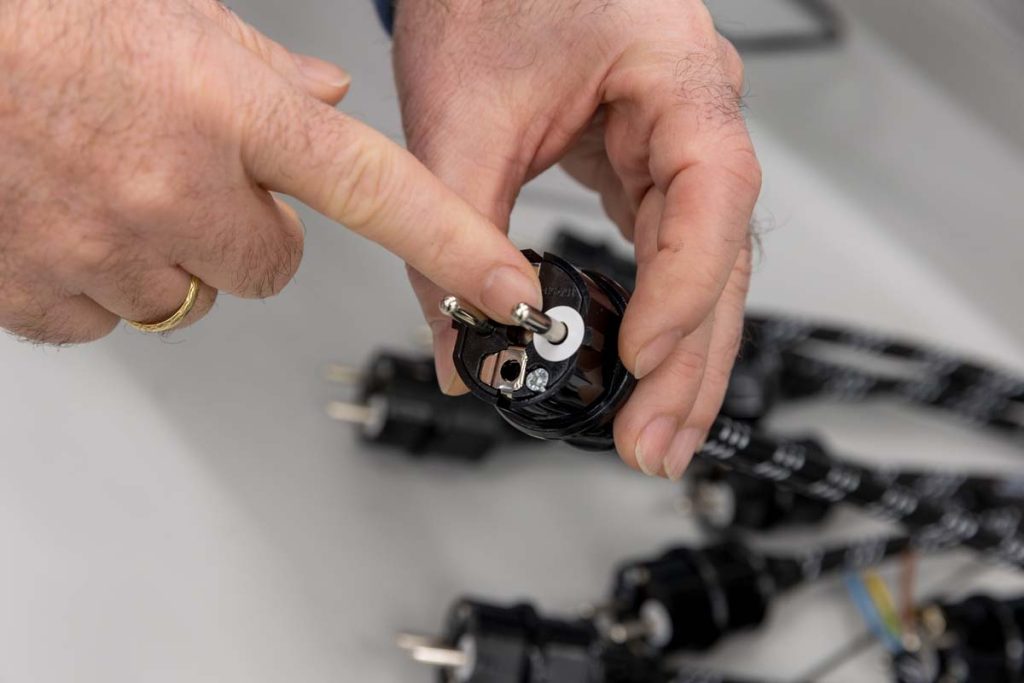
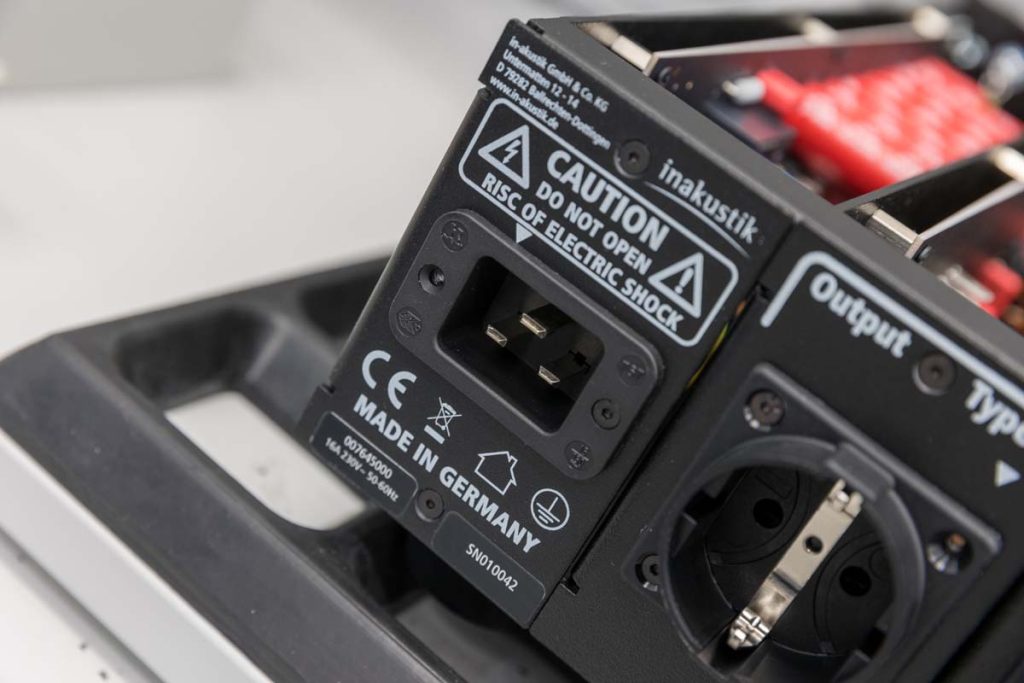
A few minutes later, we watch as the employee changes the thin wire of another piece of equipment. The outer sheath of the reference AIR cables cannot simply be cut. The complicated braiding would unravel over time. Instead, the sheaths are cut with the “hot wire.” This is precise and glues the loose ends in place. By the way, in-akustik manufactures the jackets of the more exclusive cable families themselves. Later, in a former warehouse, I witness a complicated machine that transforms some inner conductors into reference NF bulk cable with plastic tapes from dozens of “yarn spools”.
While we watch the glowing wire at work, a fridge-sized machine in our backs is busy finishing aluminum caps that a little later will cover the jackets of some finished reference AIR-NF cables. The industrial laser “mills” razor-sharp “inakustik” lettering plus the cable designation into the aluminum cups. Such work used to be done by subcontractors, Amann and Wachsmann explain. Another innovation reduces dependencies: In an alcove of the factory hall, several 3D printers are busy making hard-to-identify individual parts. These are small round structures, in this case prototypes, but the company wants to manufacture more plastic parts itself in the future. This, he says, is particularly interesting for the AIR family. To fix the complicated helix arrangement of the individual conductors in place, the cables require an “inner skeleton” of small clips. For their assembly, in-akustik has designed meter-long tables with semicircular troughs. The “basic framework” of the cables is prefabricated at fixed intervals according to the desired length, before the conductors are woven into them in concentrated work according to a fixed pattern.
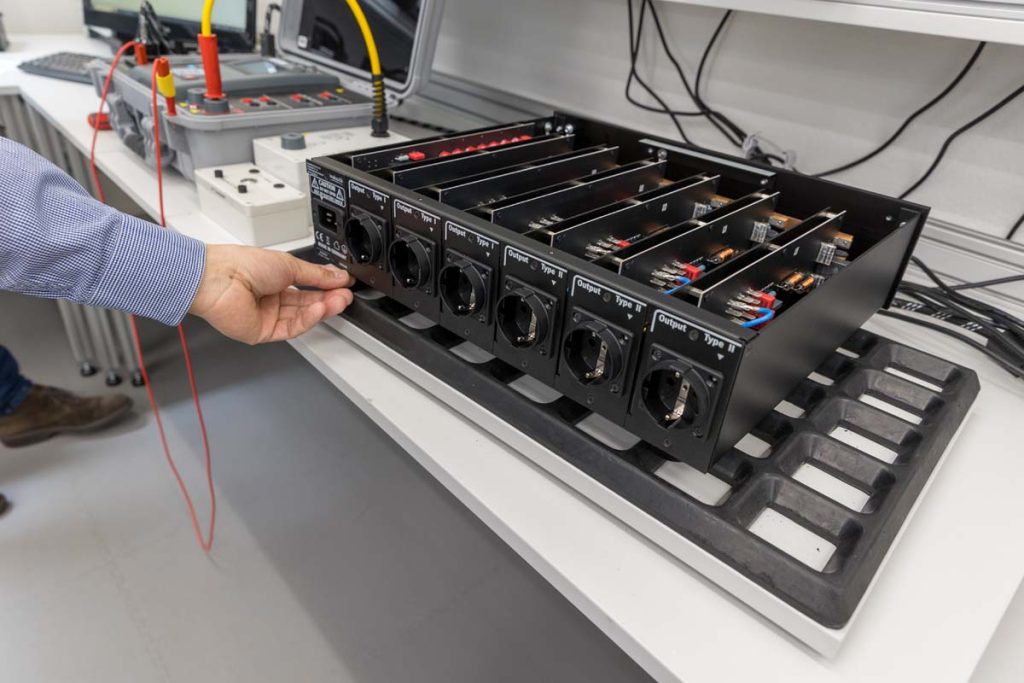
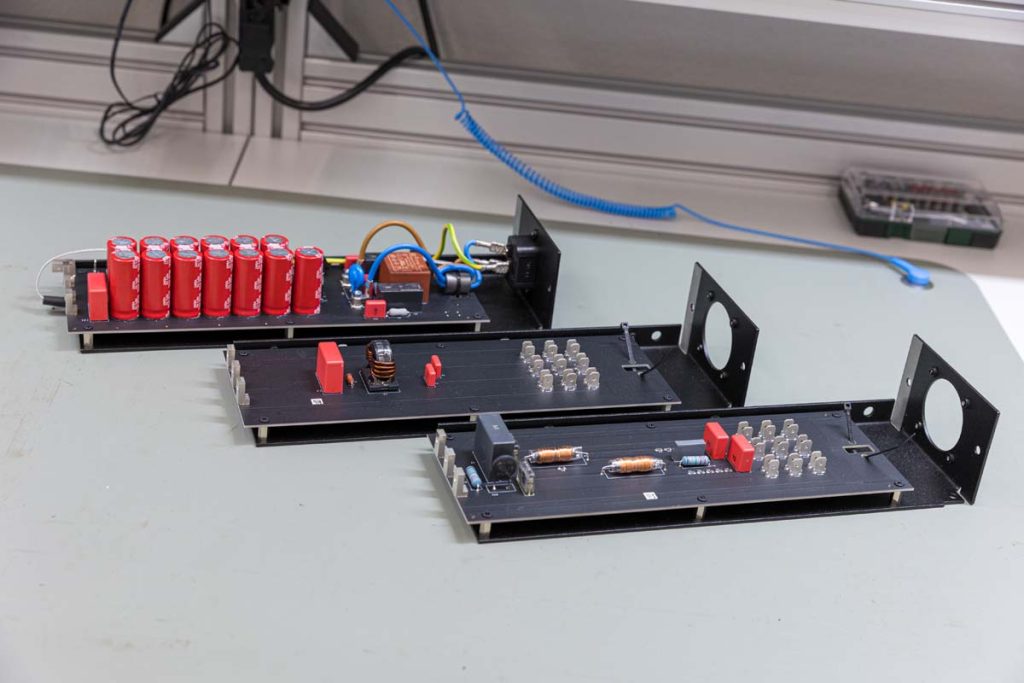
At these production tables, a small mystery is also revealed: Since entering the hall, I have heard a rhythmic whirring. I can now locate the source: a man-high server cabinet in which an electric motor incessantly bends a reference AIR power cable. The power cable, which is hung with weights, is undergoing an endurance test to check the quality of the strain relief. The transition from the Schuko plug to the cable must endure the procedure several thousand times and survive without damage. While we are on the subject, Dieter Amann points me to the small holding device on a neighboring table. After soldering, NF cables are clamped here and encapsulated with plastic. The tool for this looks like an oversized cyberpunk gun. The plastic plug created in the cable ends serves as insulation and also as strain relief.
Then it’s on to the computerized measuring station. Holger Wachsmann explains the function of the testing station to me with noticeable pride: All high-end cables have an individual barcode, while family codes exist for the less expensive strands. The employees need do nothing more than connect the finished cables, scan the code and start the measurement process. The computer automatically sets the environment variables and moments later shows whether everything is in order or whether another stop at the screwdriver and soldering iron is required. Mixing up the cable types – after all, the various AIR cables look quite similar – is thus impossible.
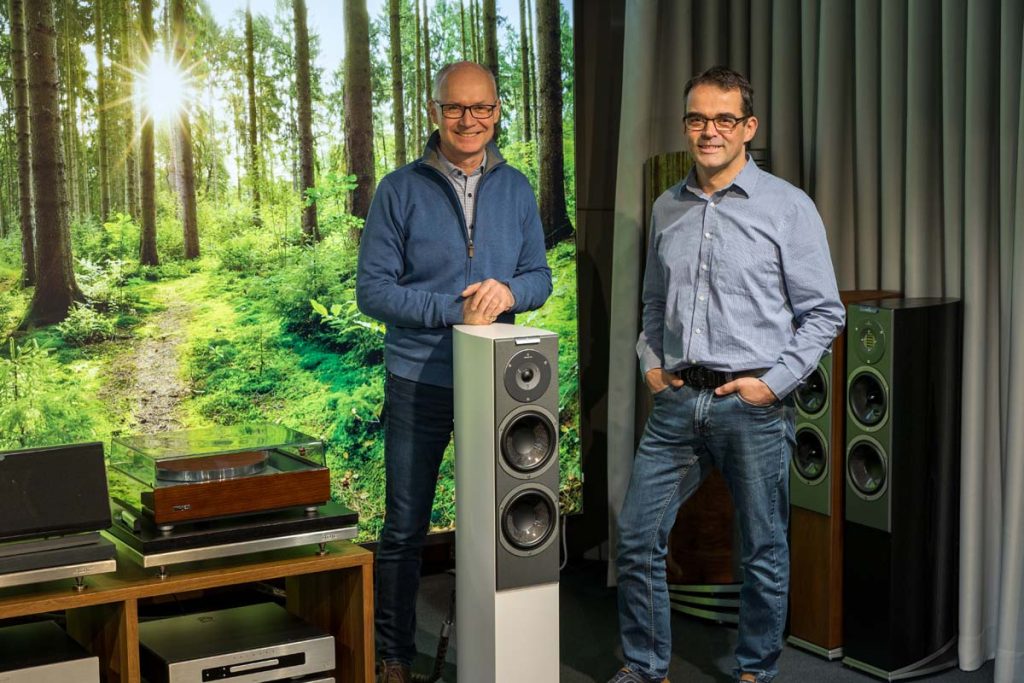
Our next stop is for the two latest stars of the inakustik brand portfolio: the AC-4500 and AC-3500P mains filters. While the “smaller” 3500 is a fixed design, the 4500 is a 19-inch rack that can be fitted with seven modules. Of course, one of them must always be the main input with its high-current power connection (IEC C20), which receives and “prepares” the power from the wall socket. The remaining six can be fitted with the differently equipped Type I modules for analog components or Type II for digital devices, depending on the customer’s requirements.
Power transmission inside the filter is via solid copper busbars. An employee is busy fitting three modules of each type into one of the metal housings. He then places the 4500 on a kind of rubber mat and begins to check the filter at various measuring points.
Our tour concludes with a look at the surprisingly large, lavishly stocked high rack storage area and the listening room, which is located in the basement of the building. In front of an artistically illuminated Black Forest backdrop, Dieter Amann and Holger Wachsmann explain to me their plans for the homely listening environment. in-akustik plans to hold workshops and events at regular intervals. The idea came up a few years ago, but was put on hold for a long time because of the pandemic. But they knew how to help themselves: Shortly afterwards, I marvel at a small video studio in the next room. Tobias Tritschler and Holger Wachsmann regularly host and moderate webinars, where they introduce a limited number of guests to topics such as “cable sound” or the influence of electricity on the system. Since the seminars work bidirectionally, guests can address their questions to the experts via chat. By the way, anyone can register as long as there is room. On the company’s homepage you can find all the information about the topics of the webinars, the duration and the number of available seats. Of course, this can’t replace the fascinating tour of the company, but it does give you a chance to get an idea of the developers’ expertise for yourself.
in-akustik
Untermatten 12-14
79282 Ballrechten-Dottingen
Phone +49 7634 56100
info@in-akustik.de