Hamburg-based distributor Audio Reference invited us to a meeting with Daryl Wilson and Dan D’Agostino in December. This is the first part of our journey through the “Wild West” of the USA.
At the beginning of our trip was a rather sleepy group of journalists. Coming from different directions, all participants met in Amsterdam at about 7 o’clock in the morning. A big Delta Airlines plane then took us to Salt Lake City, from where it was only a short drive to Provo in the south. The “little town” sometimes gets lost on maps next to the significantly larger “State Capitol” Salt Lake City. With a metropolitan population of 670,000, however, Provo is not exactly a tiny hamlet. And with an mean altitude of 1387 meters above sea level, frosty temperatures are all but guaranteed in December.
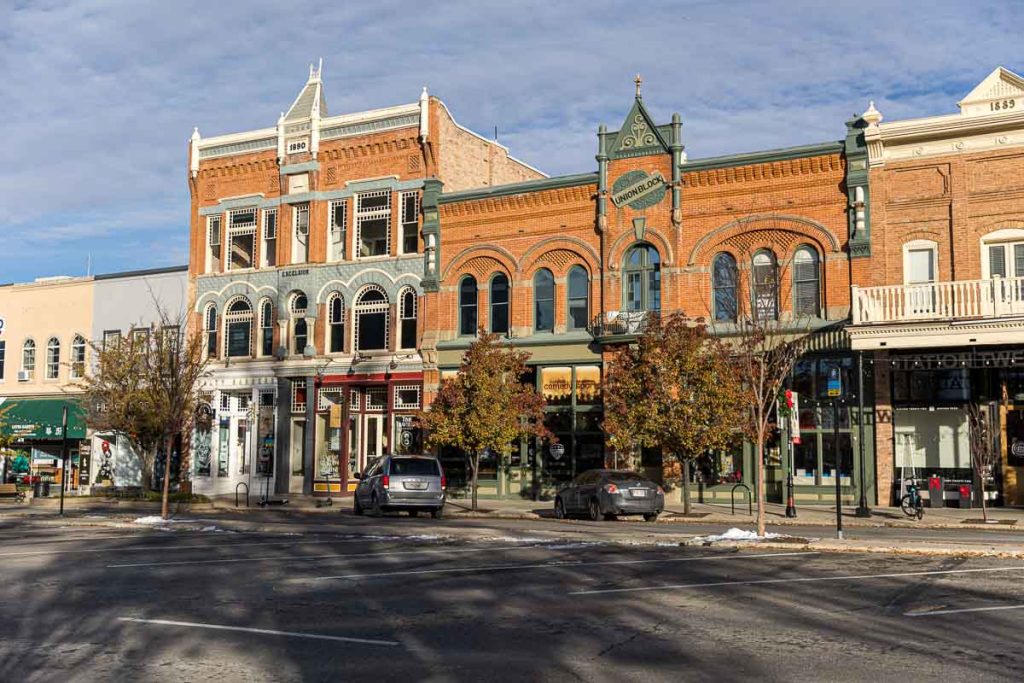
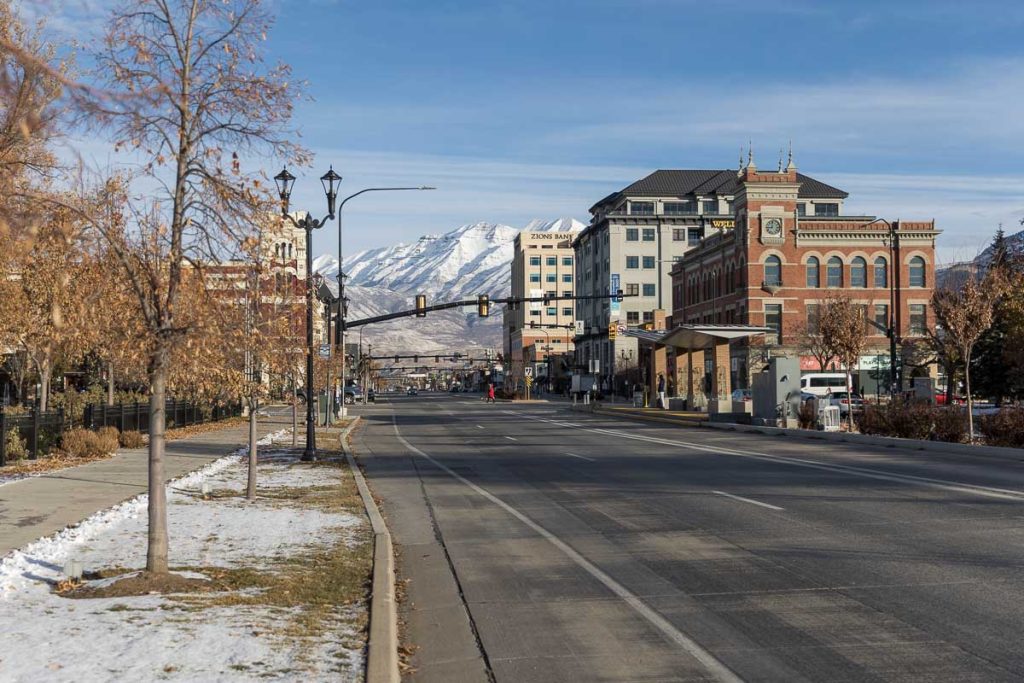
The first official appointment followed the next morning at the Wilson Audio (WA) corporate complex. Daryl Wilson, son of company founder Dave A. Wilson, who passed away in 2018, did not miss the opportunity to personally receive the visitors and, after a brief run-down of the schedule, guide them through the spacious factory halls. Besides Wilson himself, we were also joined by brand ambassador Peter McGrath, who had travelled here from Florida. He didn’t want to miss the opportunity to finally welcome visitors to the manufactory again after such a long time.
X-Material and the likes
We have already reported several times about what is quite likely the most important American loudspeaker manufacturer and told the story of the company from different angles. You’ll find the most important articles linked below. As is well known, the beginnings of Wilson Audio can be traced back to 1974. And, ironically, not with a loudspeaker, but rather turntable. Since the birth of WAMM in 1976 at the latest, though, the brand name has been firmly linked to the term “high-end”: Dave Wilson was not only uncompromising in the processing of his unique works of art, he was also among the first (and most consistent) developers to think about aspects such as acoustic timing.
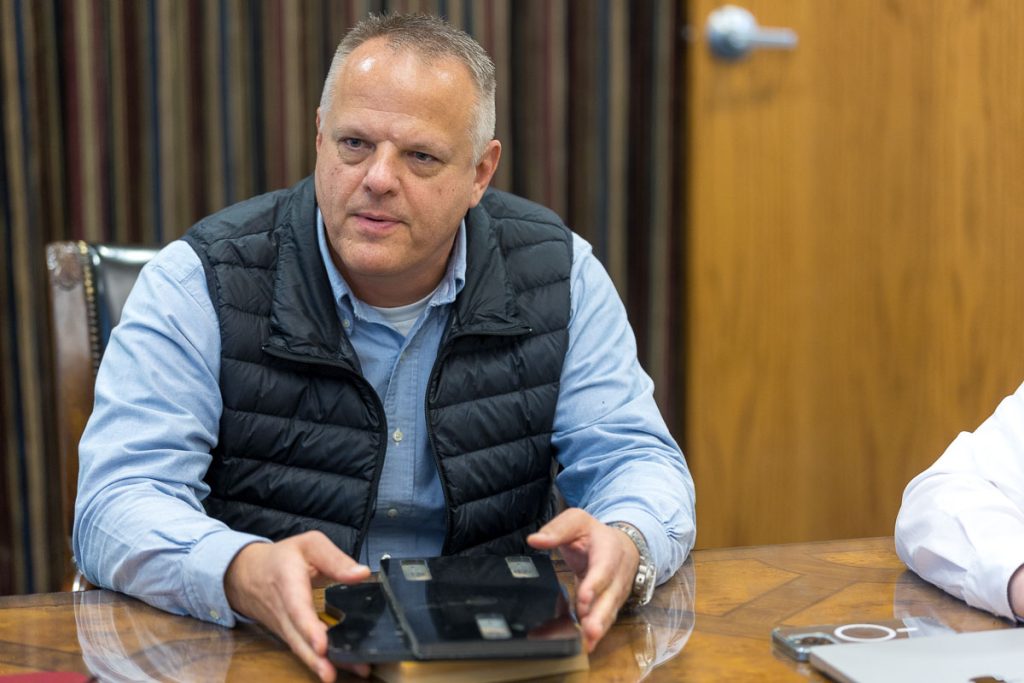
Nevertheless, barely 10 minutes after our arrival, Daryl was able to close one first educational gap (of mine): Until now, I had assumed that the mysterious “material” of the Wilson speakers was a specific variety of artificial stone. But I was wrong: Under pseudonyms such as K-, X- or V-material, the manufacturer processes several composite materials based on phenolic resin that differ noticeably in weight, density and thus also in their properties and resonance behavior. Sales manager Trent Workman illustrated this to us with a few material samples that sounded noticeably different when knocked on.
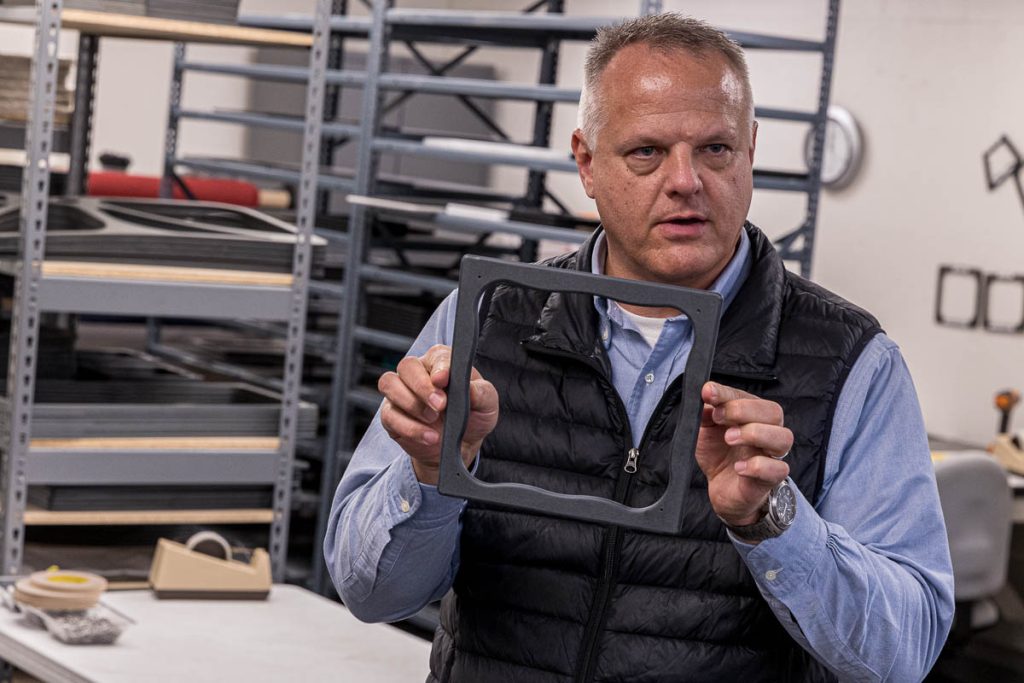
Precious Stuff
The real secret is to use the right materials in the right places. The “softer” X and V variants, for example, are suitable as damping material and vibration absorbers. The extremely hard K material, on the other hand, is the first choice for internal bracing or bass cabinets. There are no set-in-stone rules, however, since the behavior of the panels changes with their size and the recipe of one loudspeaker cannot be transferred to another without further ado. Decades of experience make it easier to work with the materials; whenever a new variant comes onto the market, it is at least tried out. And one piece of information on the side, which was also new to me: Even the support frames of the fabric-covered speaker covers at Wilson Audio are made of the precious material.
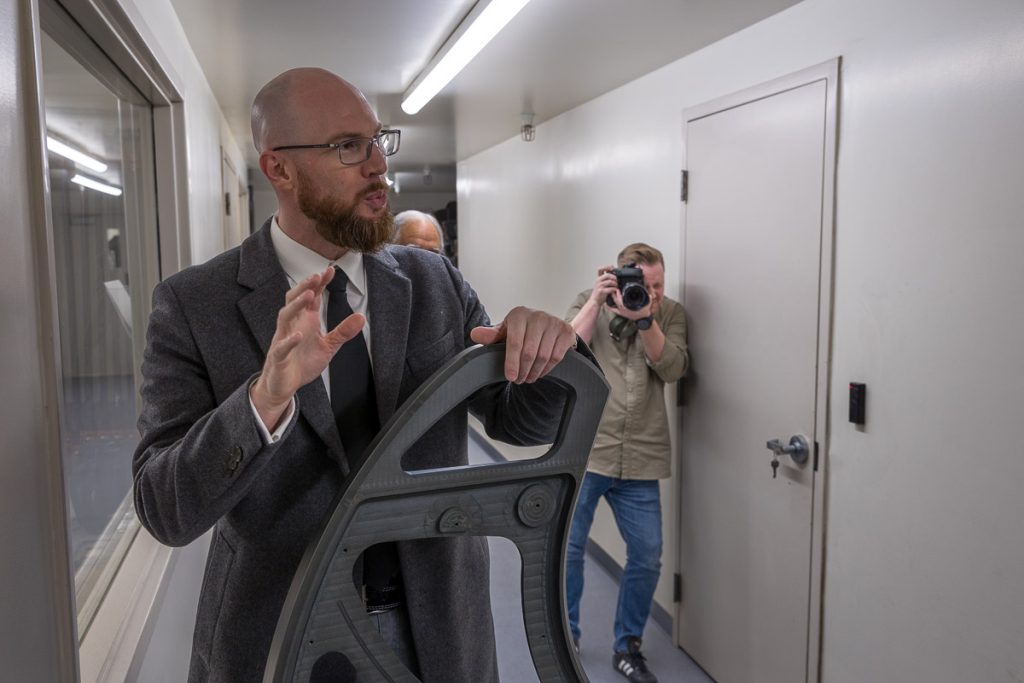
In one of the countless aisles, we discover a whole stack of freshly delivered “stone slabs”, which Daryl took as an opportunity to explain the prices of his speakers, which can be exclusive indeed. Even the smaller of the massive slabs cost the company over $500 to purchase. Even simply constructed speakers like the comparatively tiny TuneTot require six of them. Despite computer-controlled cutting of the material, the waste is enormous. And so is the processing effort. As our tour continued, we stopped in the milling and assembly hall. Here, two huge machines are incessantly busy shaping the composite. Their diamond-hardened milling heads have a maximum service life of two hours with the unruly material. After that, they can be sharpened by a service provider and, after another two hours of use, they finally go into the recycling bin – we were able to examine a few drums of used milling cutters right in the hall.
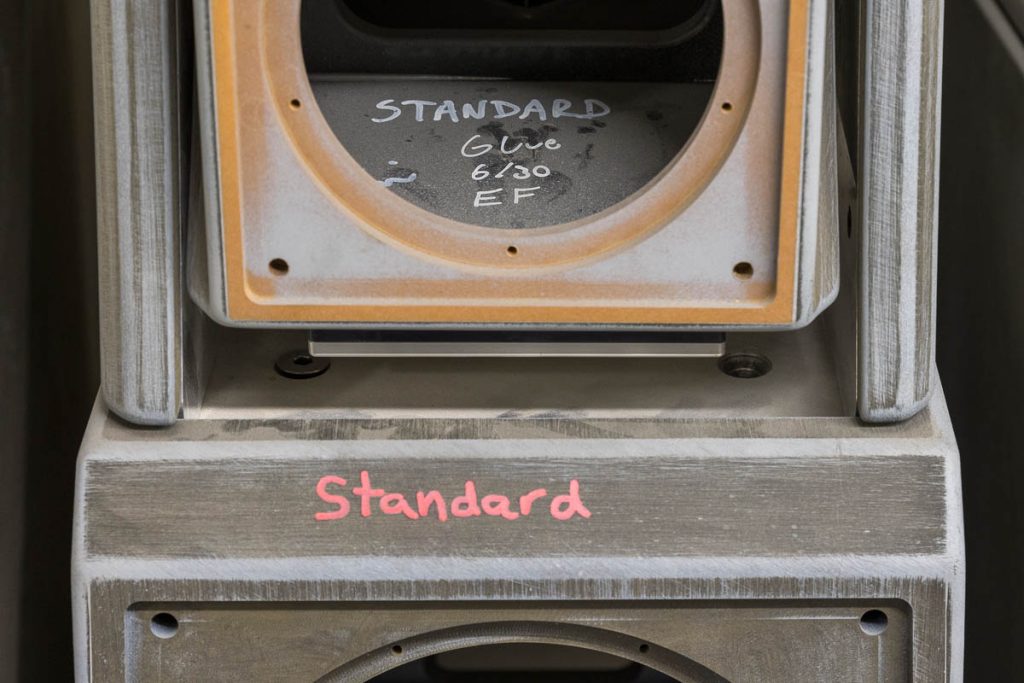
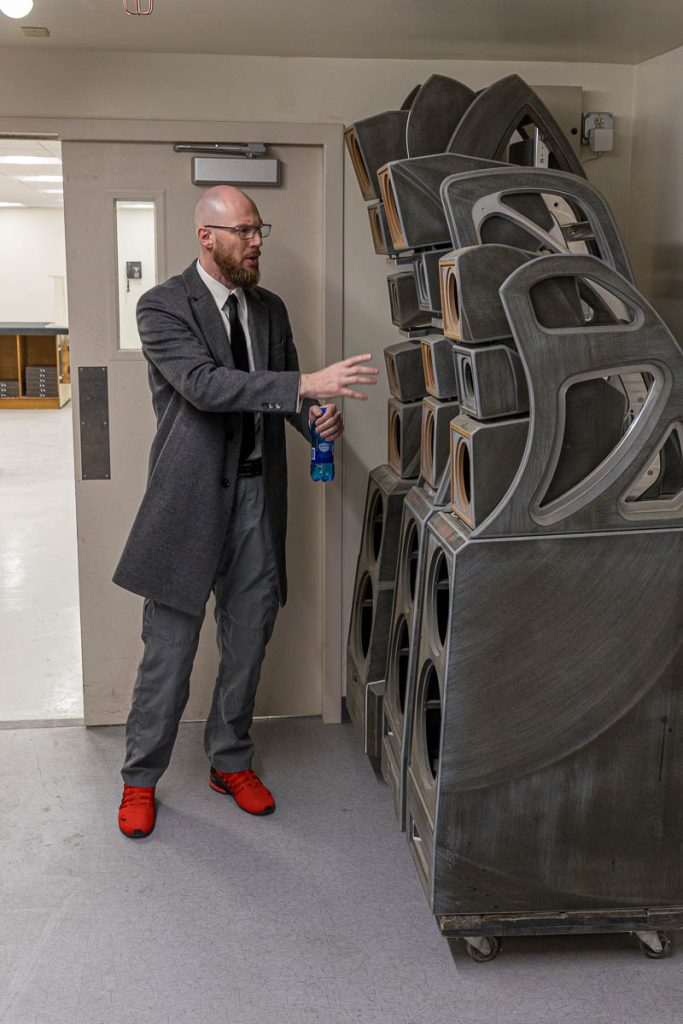
Milling And Gluing
In the immediate vicinity of the machine park, two employees were busy transforming the cut panels into the bass enclosure of an Alexia V. The speakers are completely glued. This is precisely where the manufacturing process of a Wilson Audio speaker changes from CNC precision work to a manufactured product: The two employees meticulously checked the result of each individual gluing, placing marks here and there for the coming processing steps. No sooner had they finished the bass cabinet than they signed the component at designated positions inside. Each individual production step is documented and noted on the speaker. From the first assembly to the final polish, quite a few signatures come together …
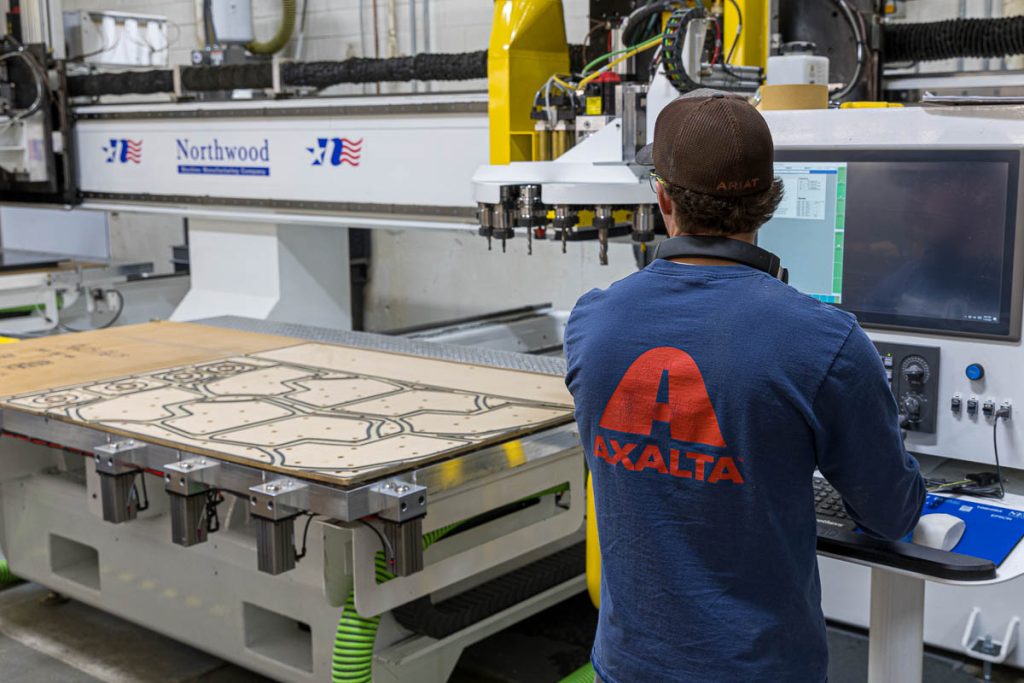
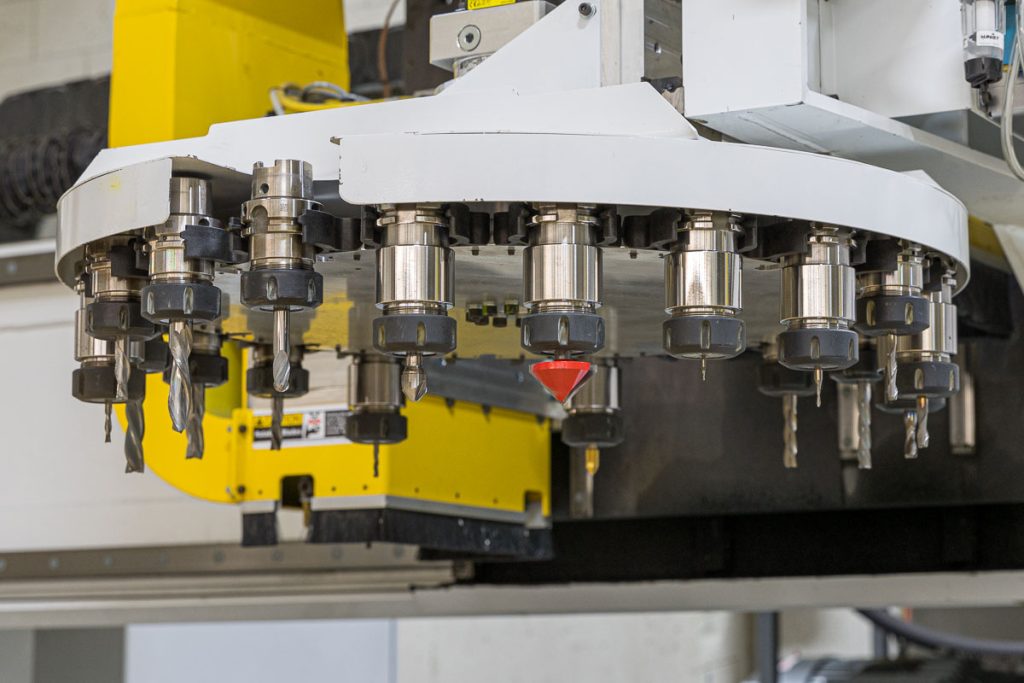
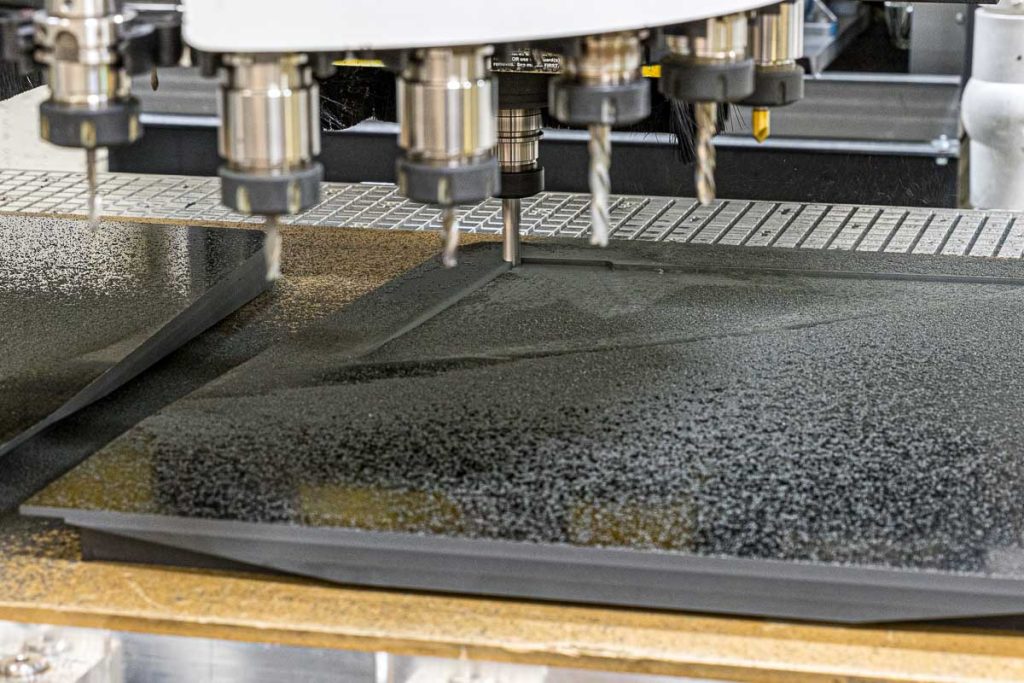
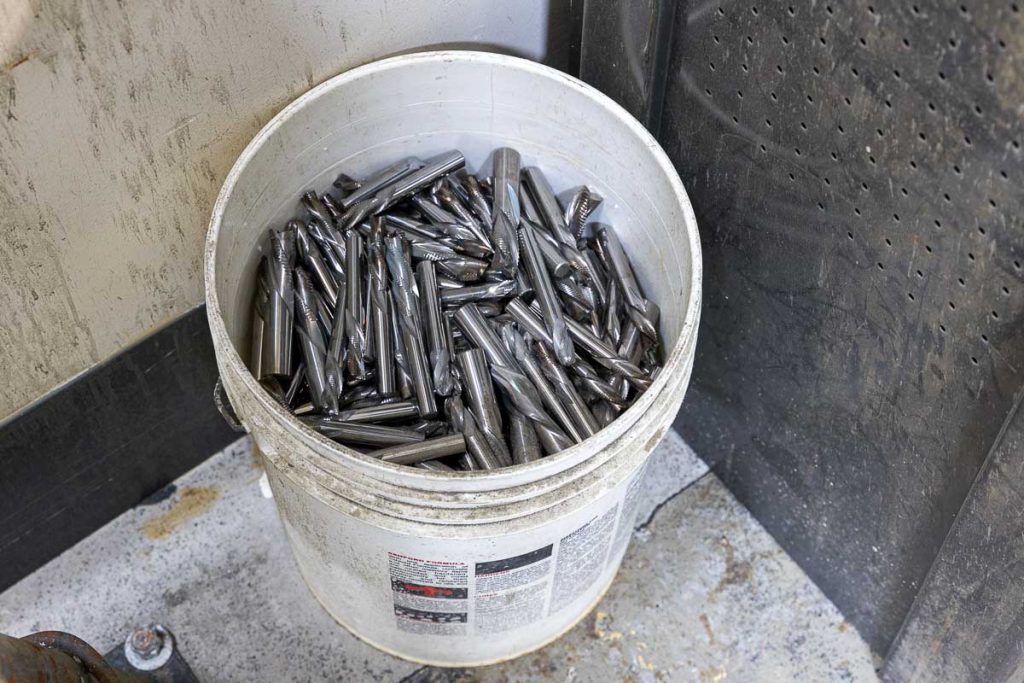
The next stop we made was the preparation for the paint shop. In this special sanding room, the still comparatively rough cabinets are brought into shape and smoothed. A whole team of employees removes protruding edges and glue residue. Since the inaccuracies can vary greatly, they have a sometimes obscure park of sanding machines and jigs at their disposal for this purpose, which they use to prepare the raw bodies for paint application.
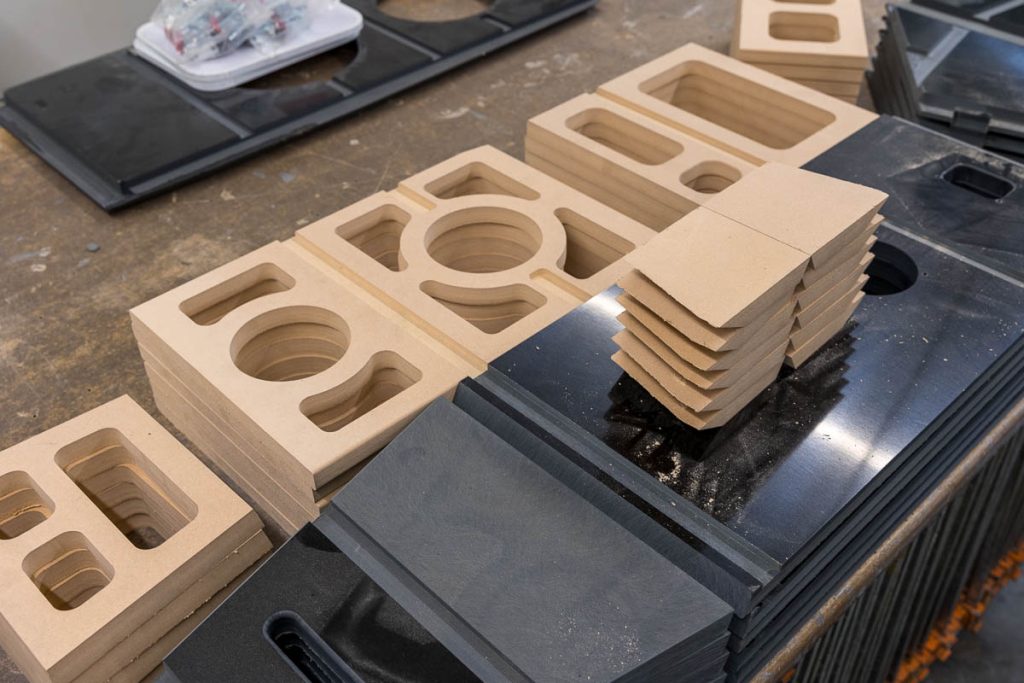
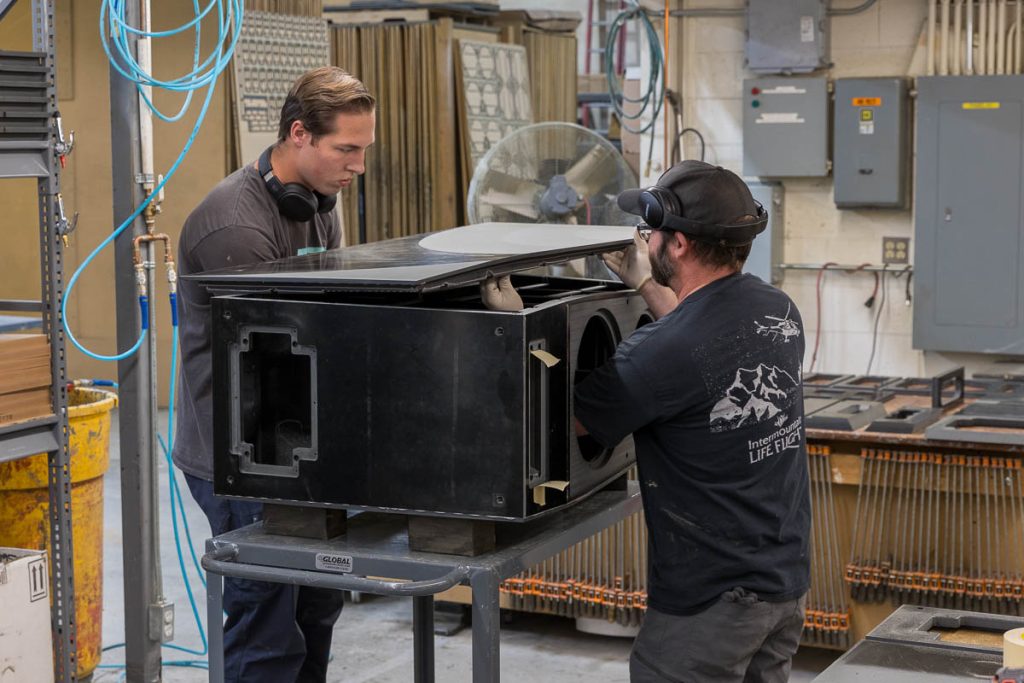
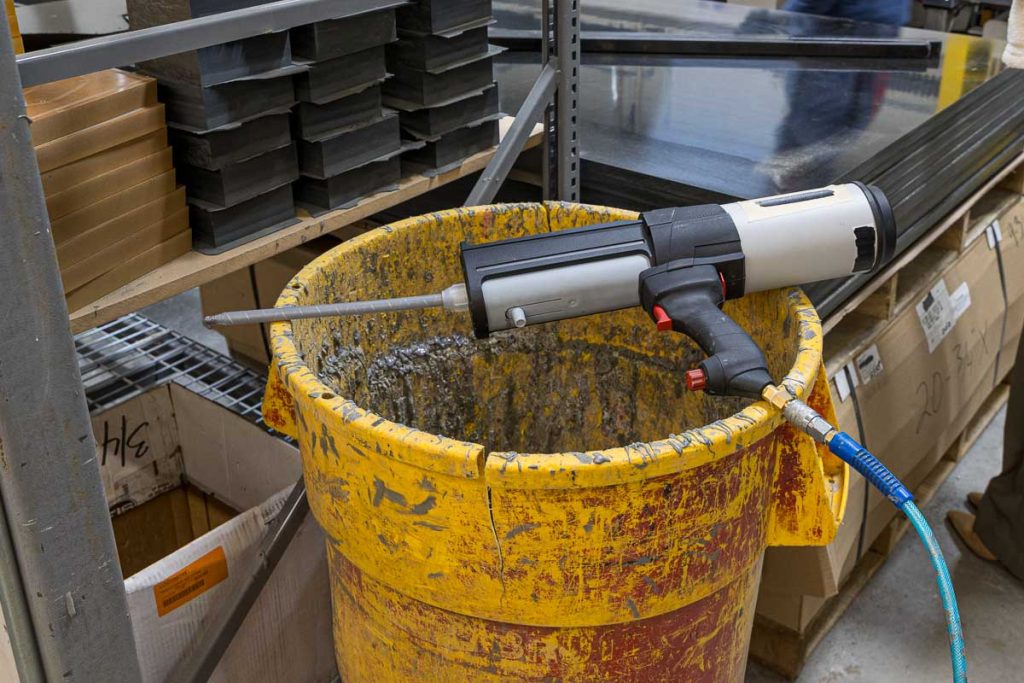
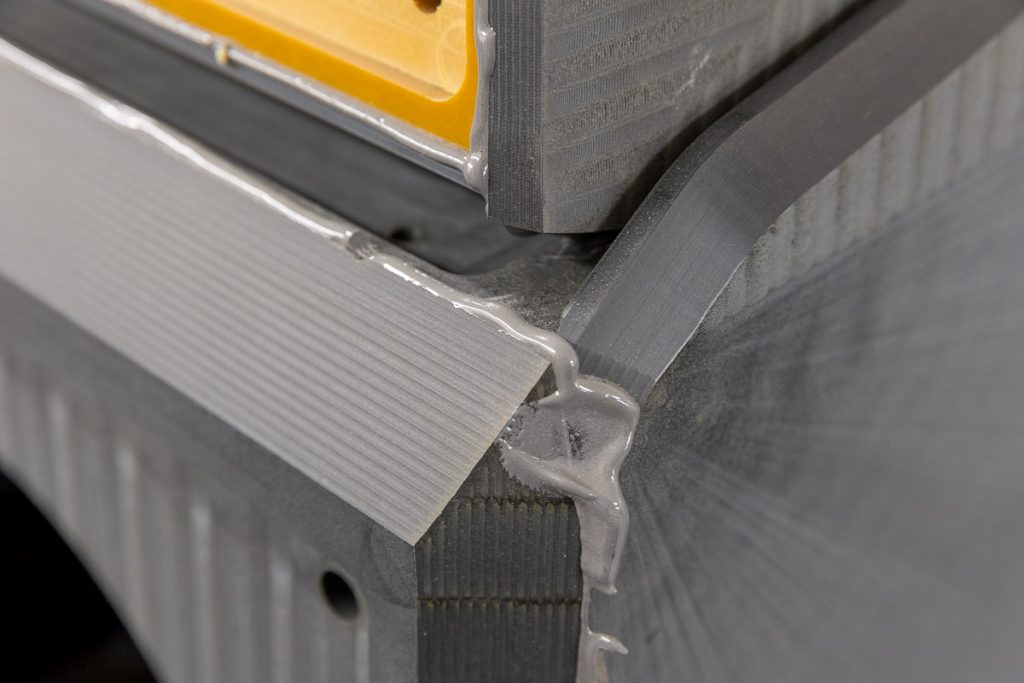
Bringing Color To The Game
Wilson Audio is notorious for its outstanding finishes, and we can now see why: each component of the speakers – most speakers, after all, consist of several segments – is primed, sanded, painted, sanded, painted again, sanded, and so on. Finally, the segments are polished, where they are again given a deep, high gloss finish in several steps. Several weeks of work go into the newer effect paint variants in particular, as the paints have to rest again and again for days – in some cases even weeks – to cure. A particular challenge was to construct the building complex in such a way that the dusty sanding shop and the painting separees interlock directly without interfering with each other. This is made possible by a separate annex with high-performance ventilation systems and an air-conditioned rest area where the coatings can cure in perfect peace.
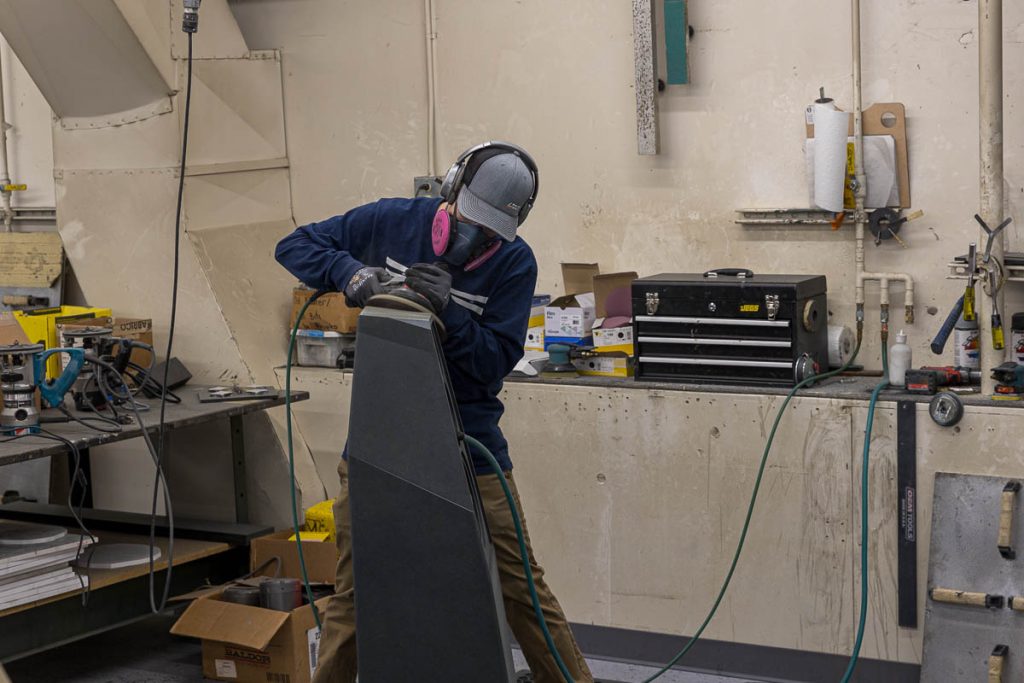
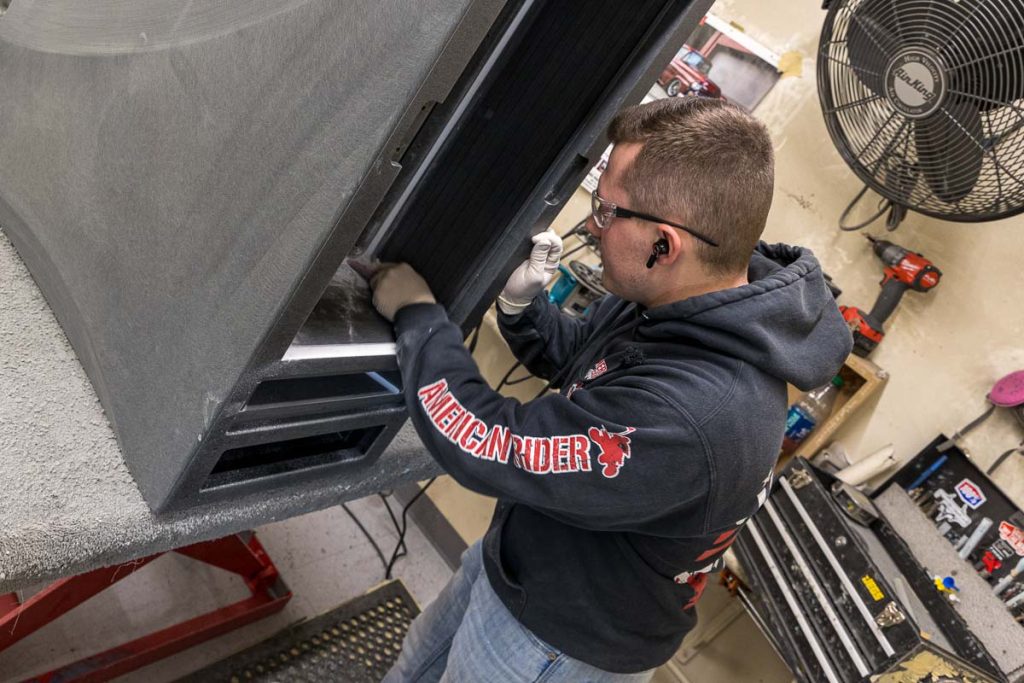
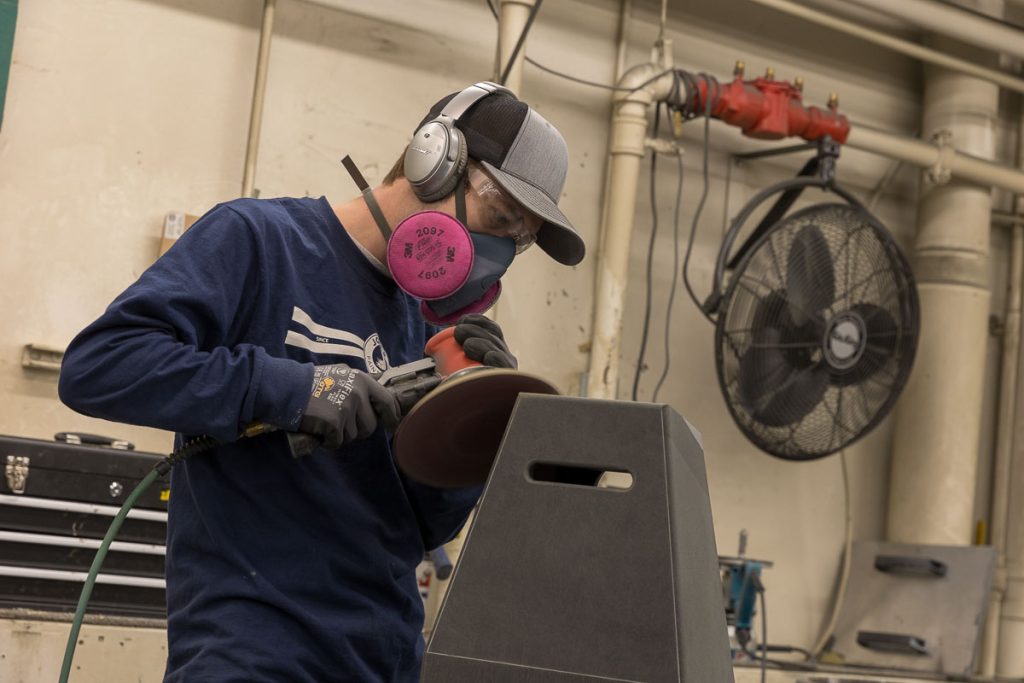
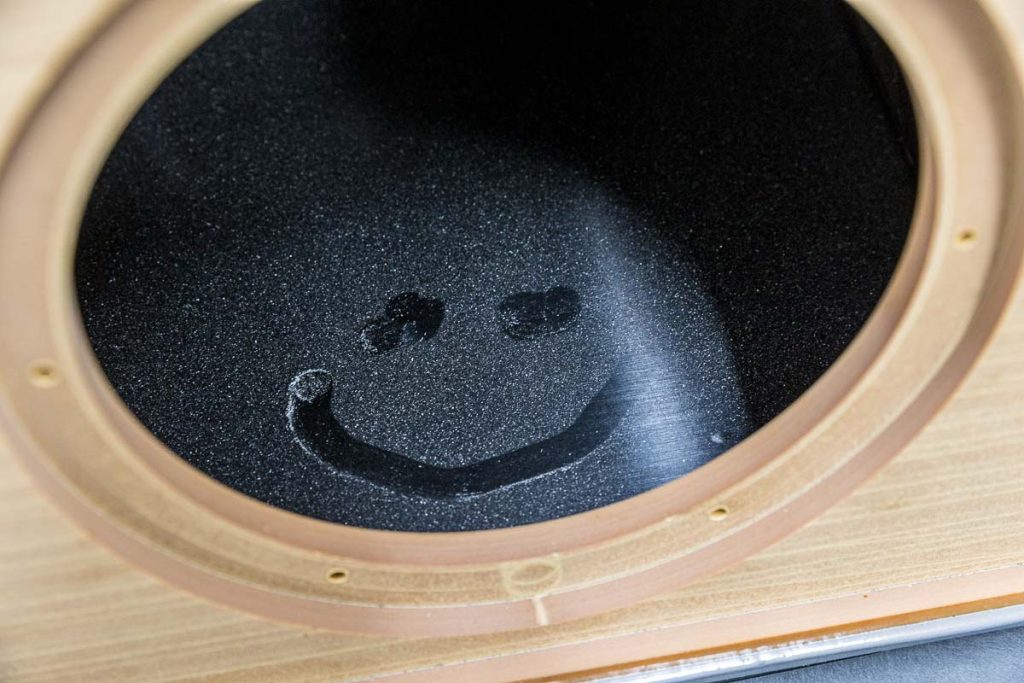
Directly after this area, we were introduced to the final assembly, where we could for the first time lay our eyes on drivers and electronics. Half a dozen employees were busy making cables. Wilson Audio produces all the internal wiring itself. This is the only way to ensure that all connections achieve the required quality. The same applies to the components of the complex (and sometimes huge) crossovers. In order to become more independent from the selection and quality of suppliers, the company recently acquired its own capacitor production. The production takes place in some adventurously complicated-looking machines. The wound coils are then sealed with various glazes and vibration damped.
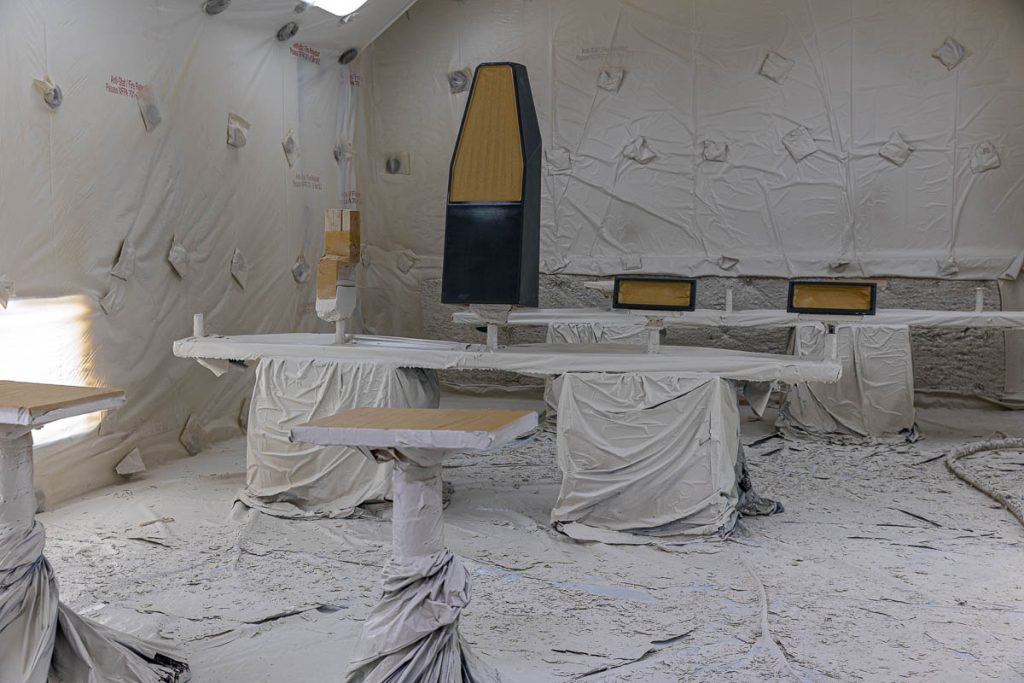
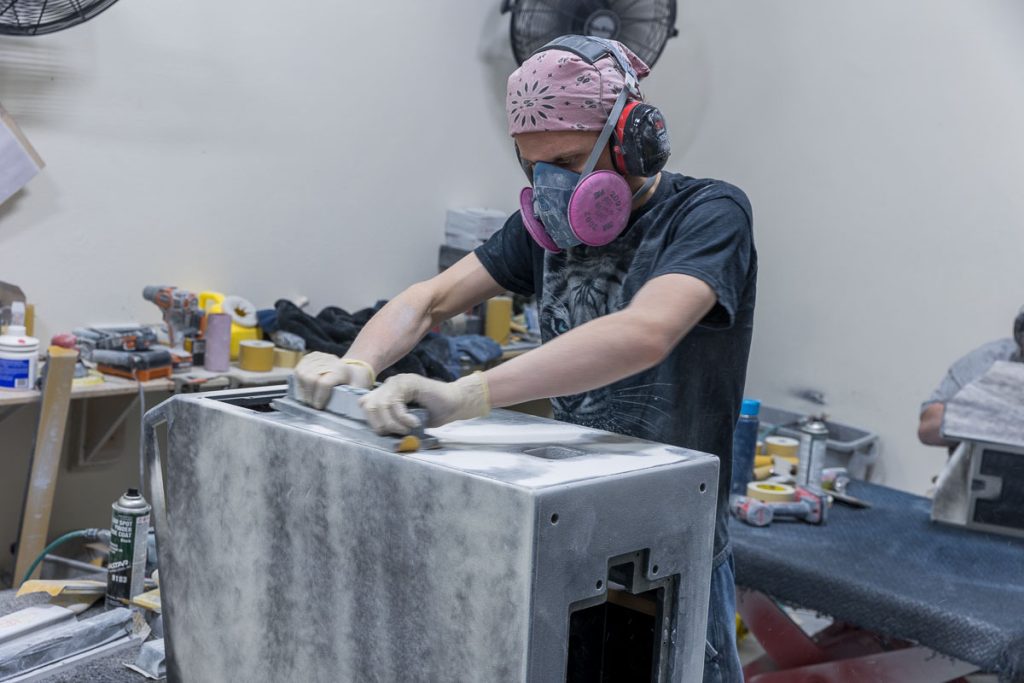
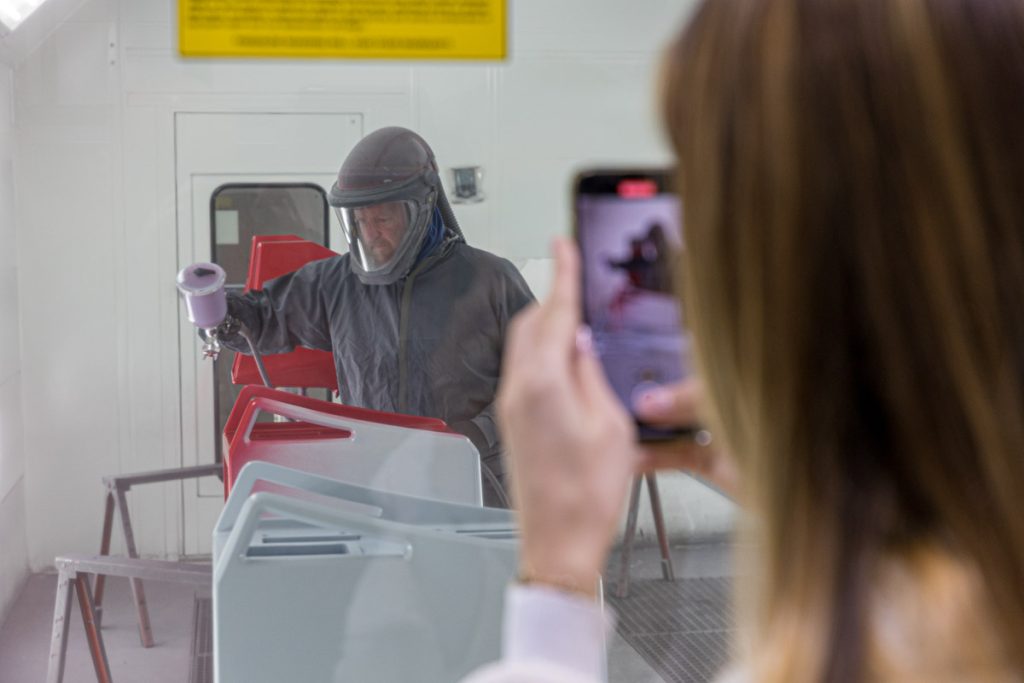
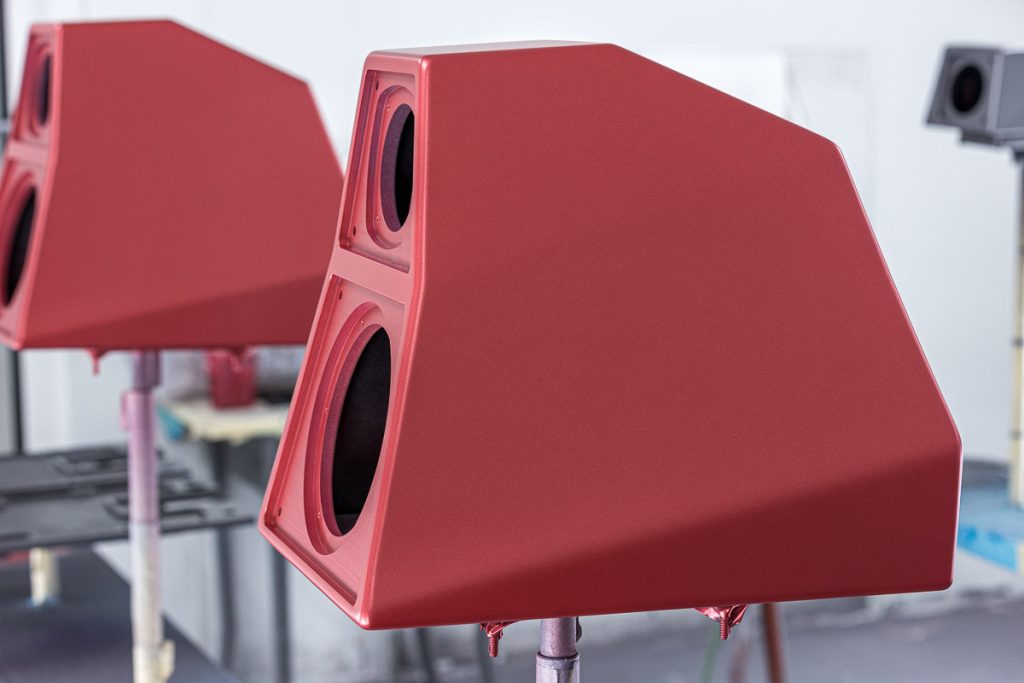
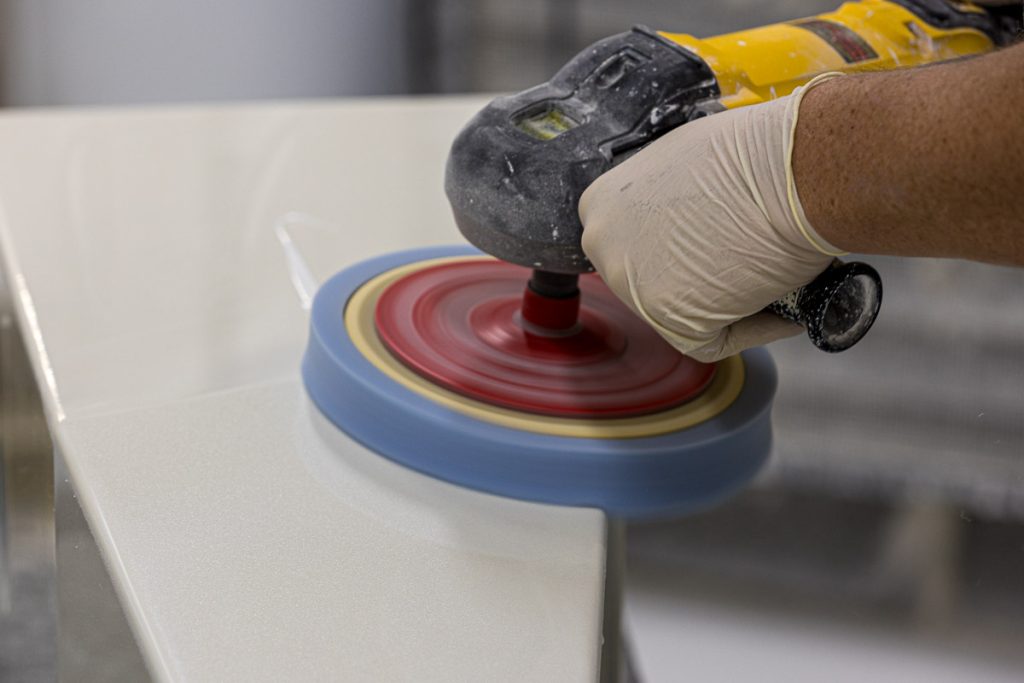
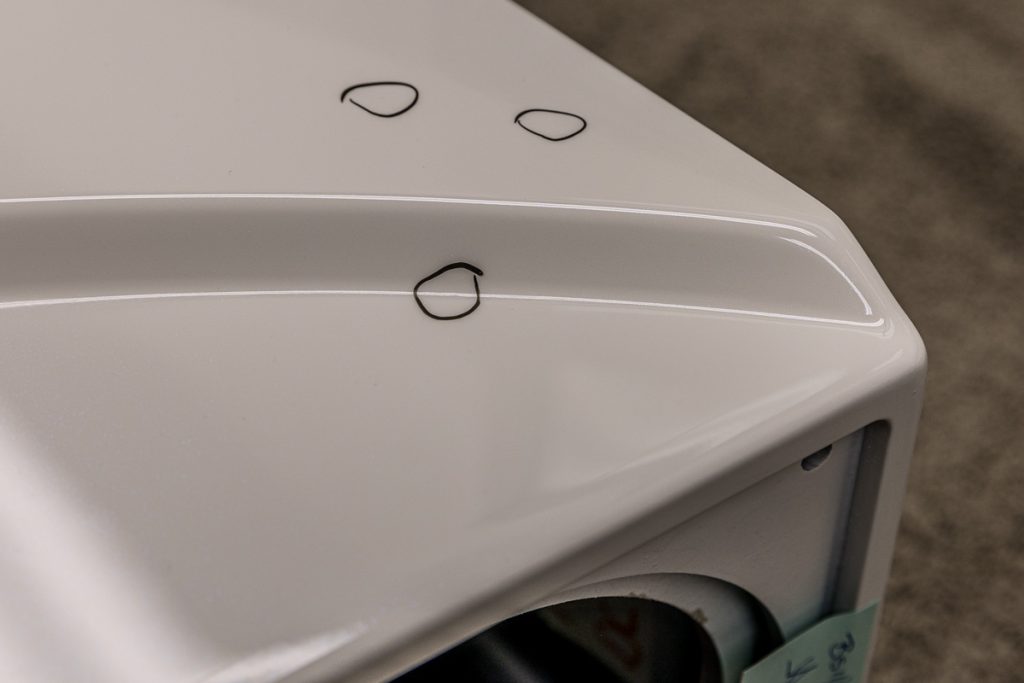
In-House Development
At the end of our tour, we took a short trip to the development department. In a small “infernal chamber” we experienced the effort Wilson Audio puts into its drivers. Some bass drivers were undergoing endurance tests, others were just being prepared for this procedure. To my surprise, I also spotted some driver variants that Wilson Audio does not (yet?) use in its speakers. Obviously everything is tried out. We got to know a particularly cute detail just a few rooms away: WA owns several 3D printers that are used for “prototyping”. Tiny to medium-sized speaker studies can be found everywhere in the development: models of the Sasha DAW, dinky Alexias, filigree versions of the XVX and so on.
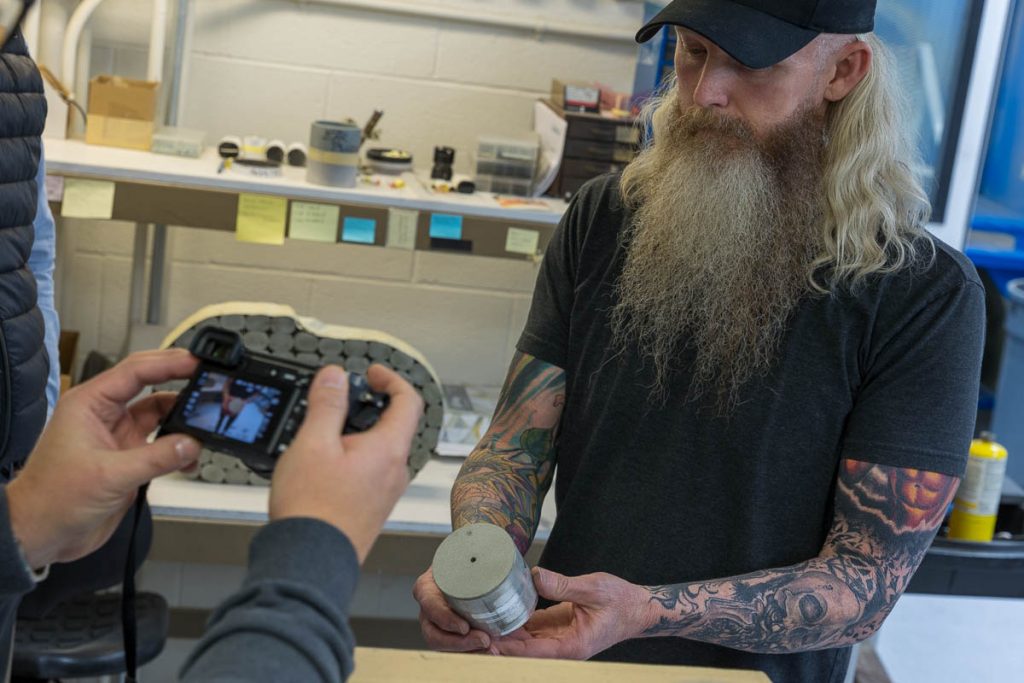
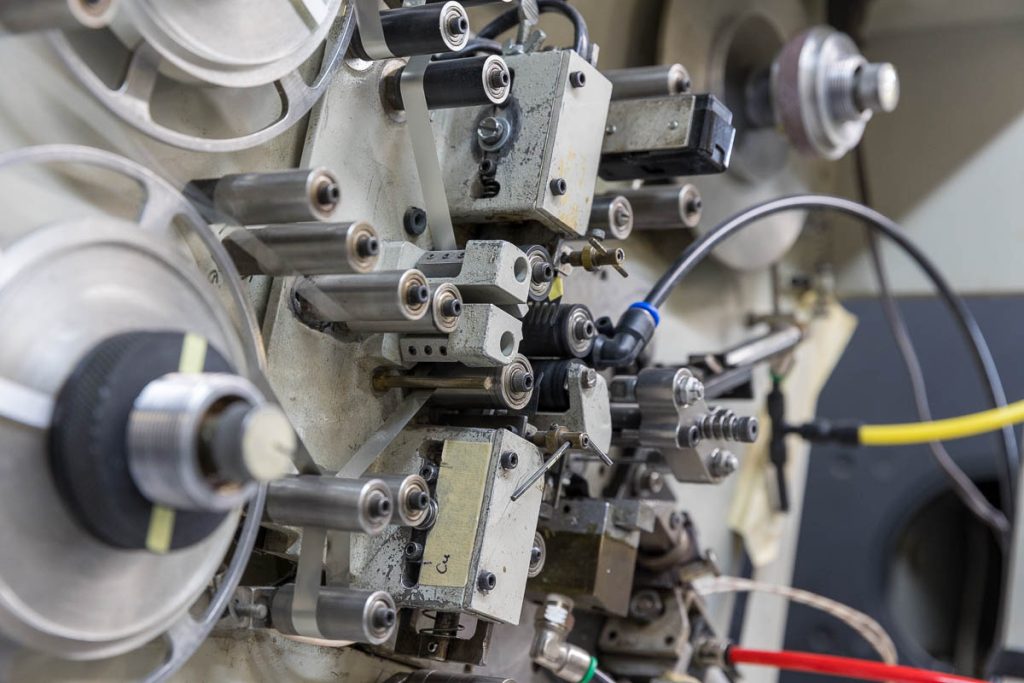
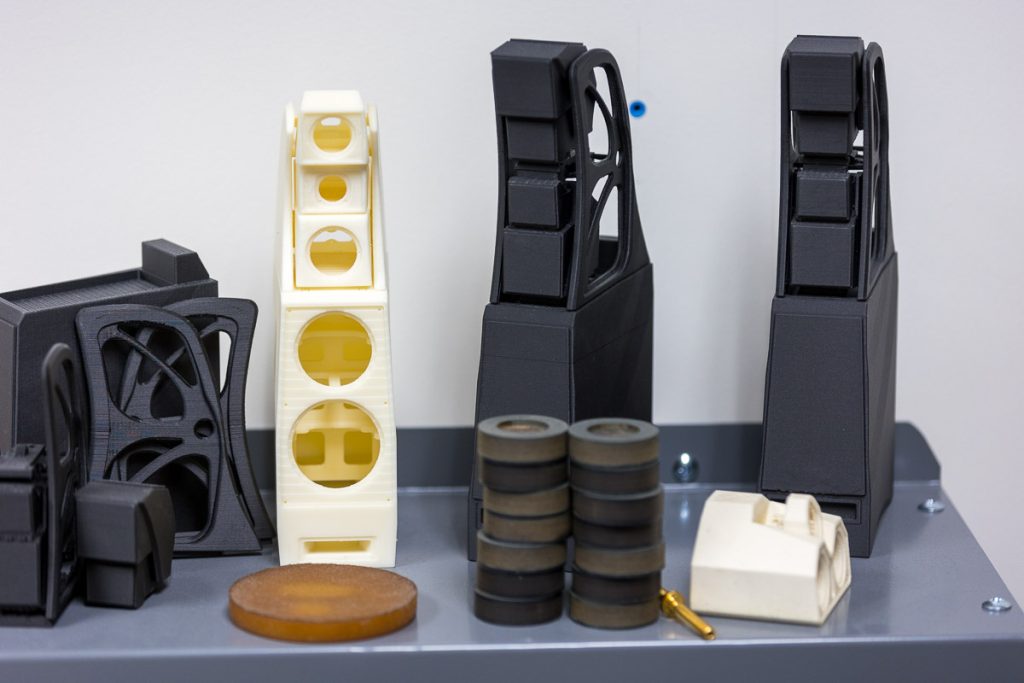
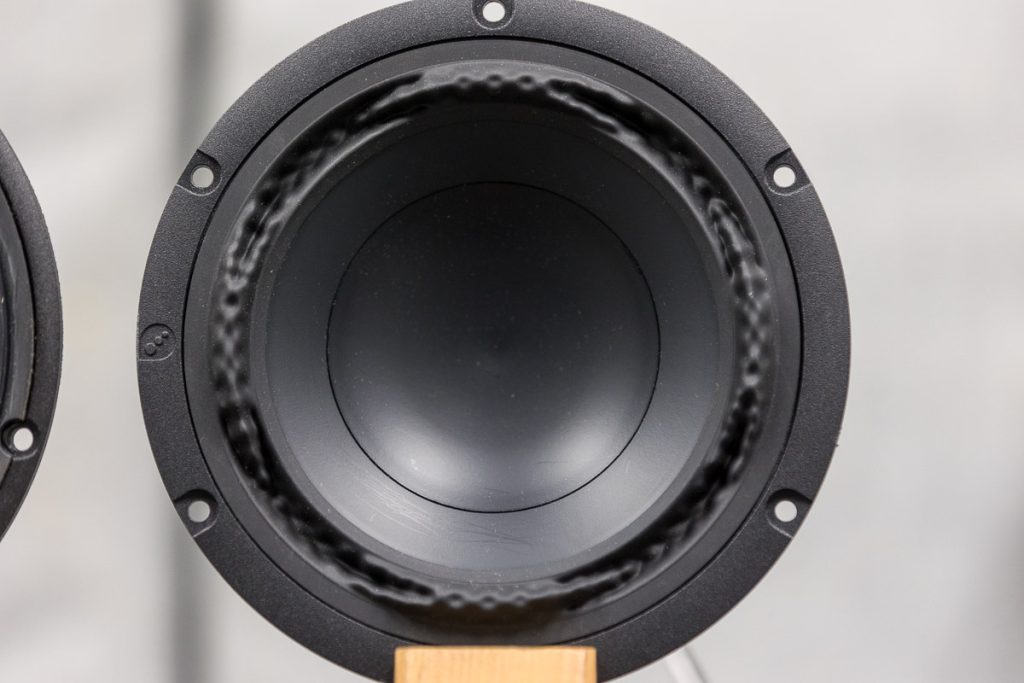
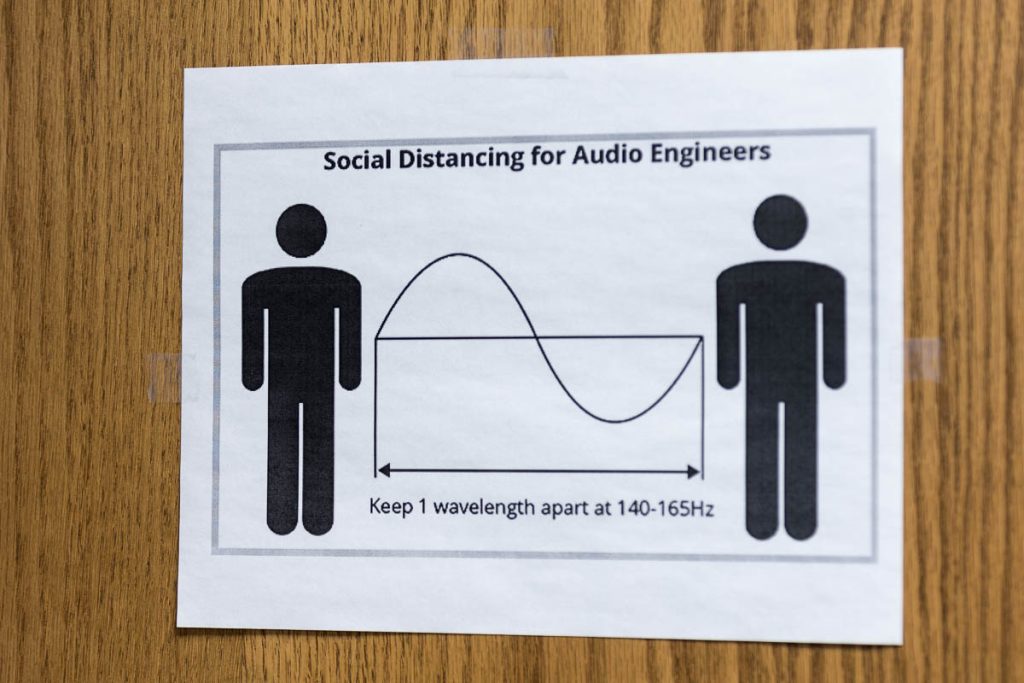
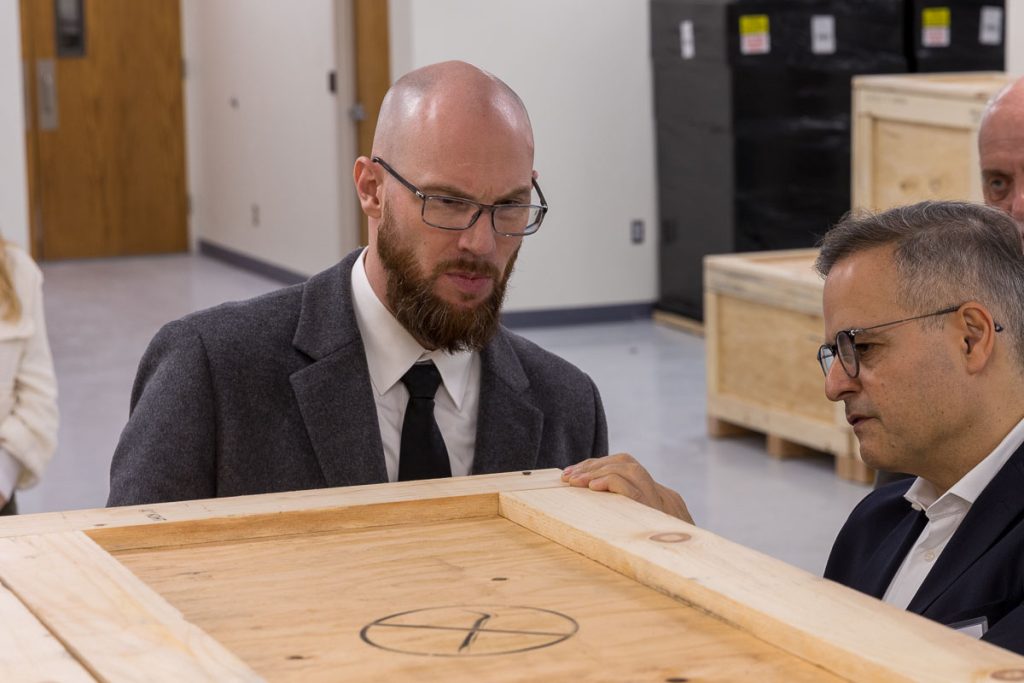
Over Coke, water and salad, we then had the opportunity for some small talk. Daryl told us about the challenges of the Covid period, which his company had mastered satisfactorily. In contrast to many other companies in the vicinity, Wilson Audio did not have to lay off any employees. He said that in-house component production in particular proved its worth during this time, as it reduced dependence on supply chains.
His father left him a healthy company with both feet firmly planted in the hi-fi industry. He himself (Daryl had been involved in all developments for over twenty years) has the traditional series well under control. Above all, however, the approaching anniversary makes him pensive – in 2024 WA will turn 50 years old. It is a huge challenge to make Wilson Audio fit for the coming decades. And the hi-fi market is currently undergoing a profound change, which makes the planning of future products considerably more difficult …
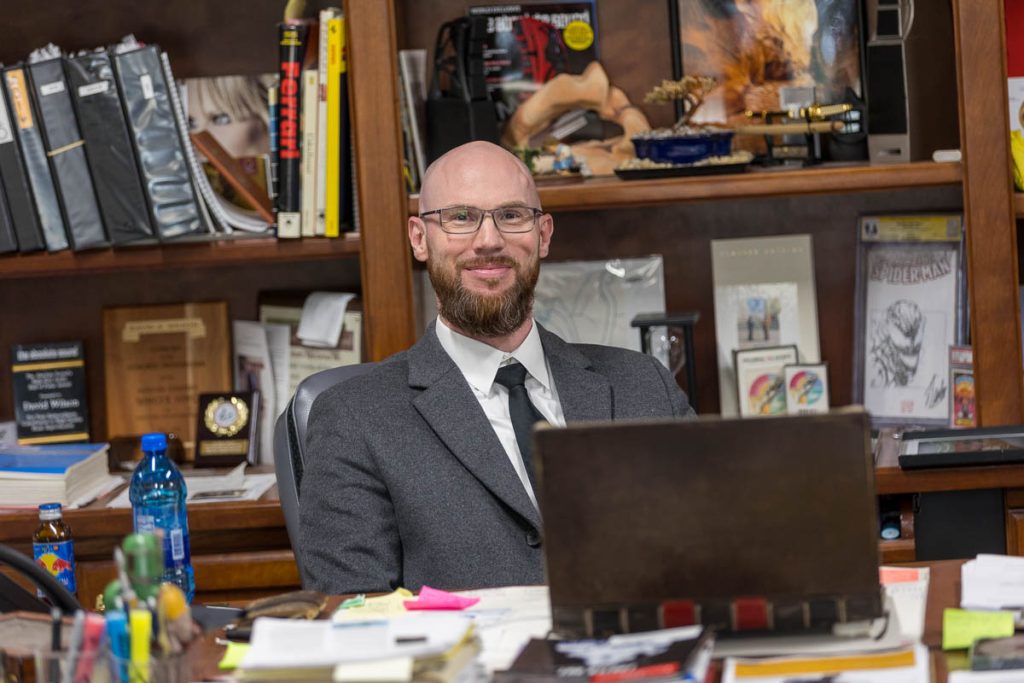
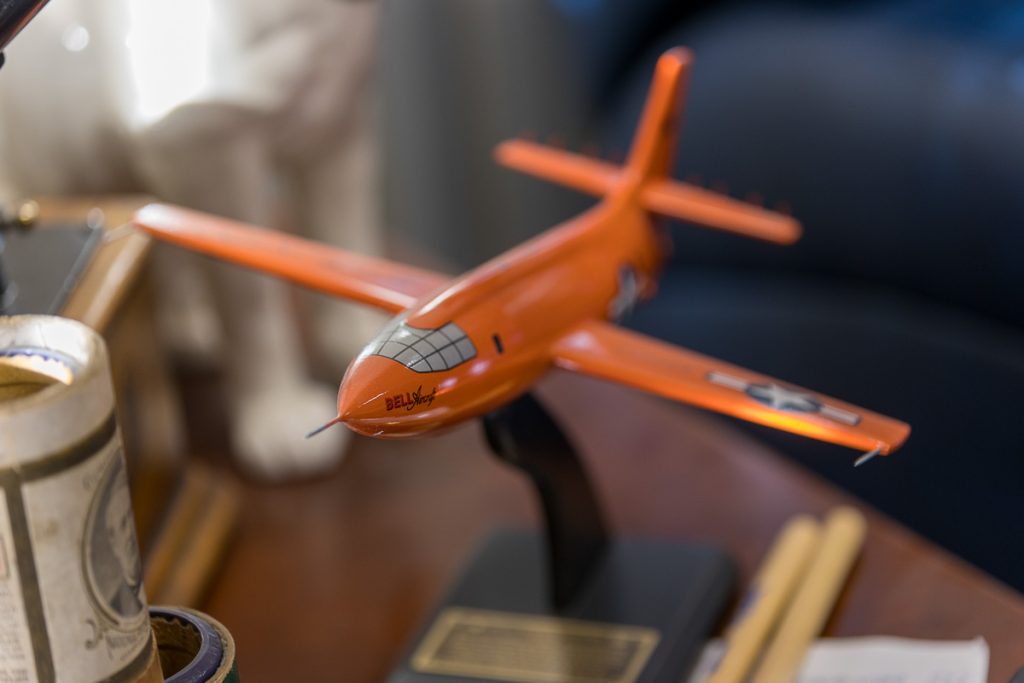
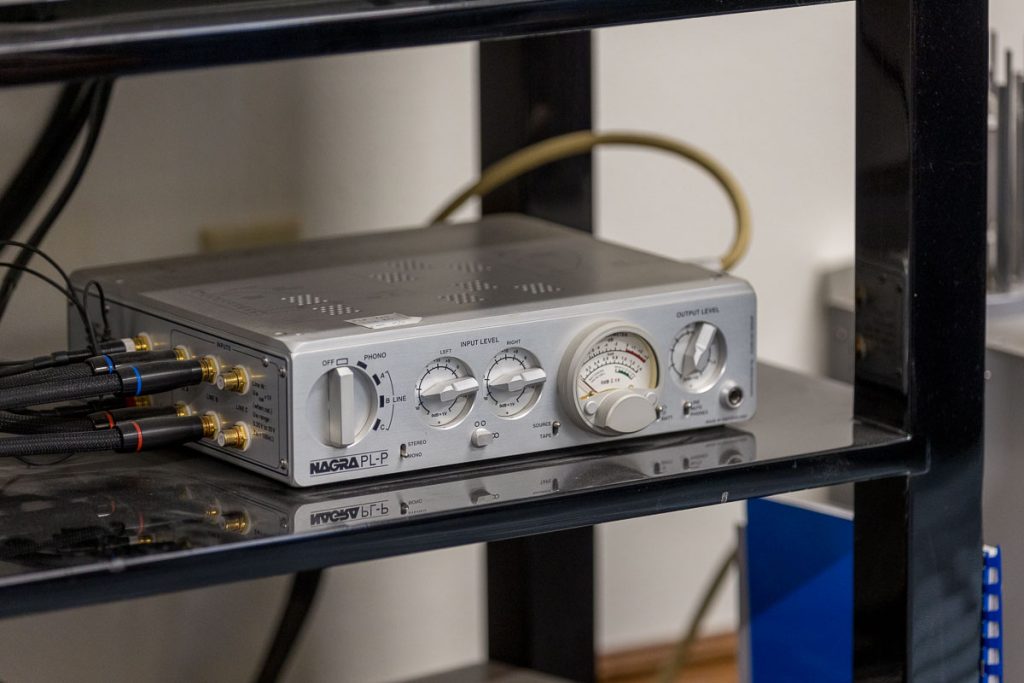
Daryl Wilson Presents The WAMM
The rest of the day, however, was once more dedicated to the company tradition. Daryl Wilson invited us to his parents’ house, where we met his mother Sheryl Wilson. The Wilson’s living room is still the best place to experience the mighty WAMM Master Chronosonic. After all, the colossus was developed within these four walls. Over the next few hours, the speakers with their two subwoofers gave us an impression of true elemental forces. Peter McGrath demonstrated some of his own recordings to us, which conveyed a glorious live atmosphere and showcased the sheer limitless soundstage of the WAMM. Daryl then revealed to us that the homely room was constructed to the specifications of a recording studio. Although the room appears rectilinear, there are no parallel walls, he said. Invisible absorbers are built into the ceiling.
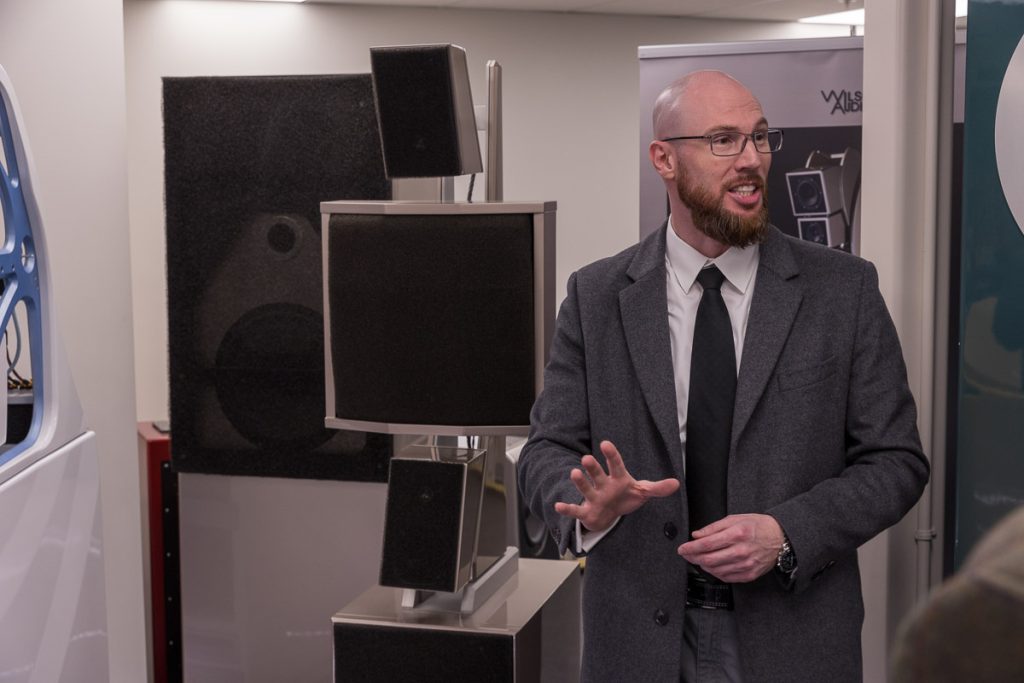
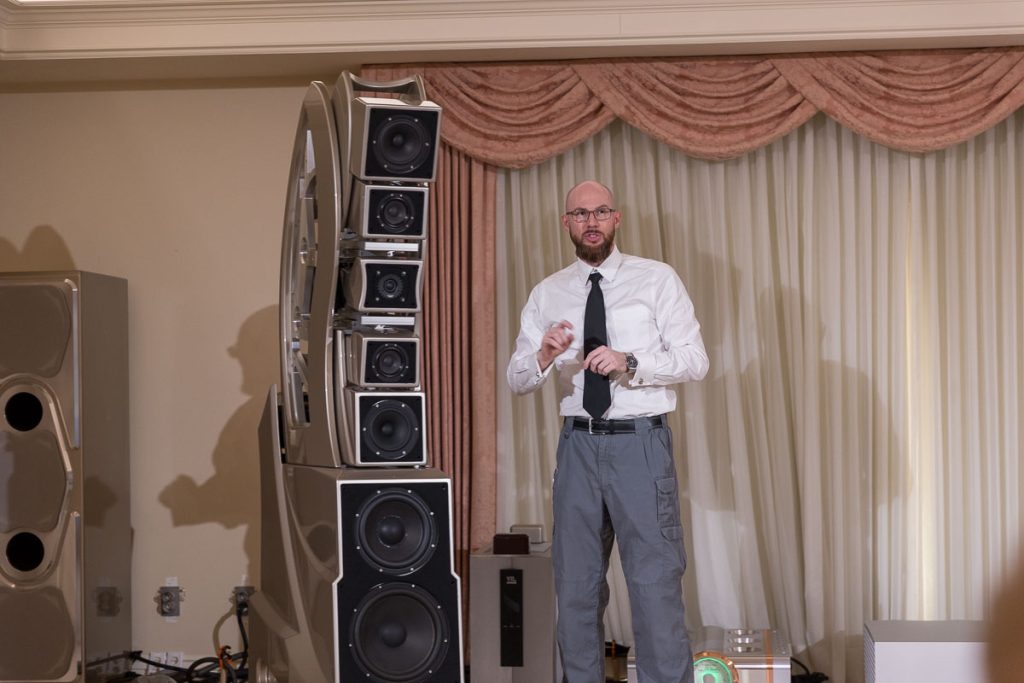
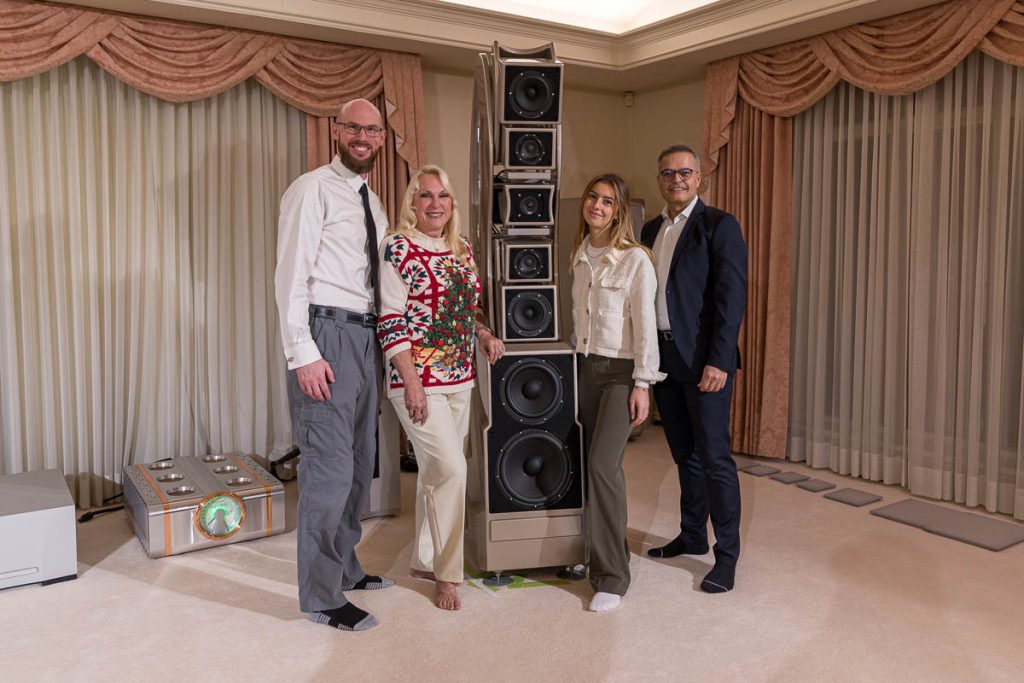
The next morning, the journey continued to our next stop. But what we experienced at Dan D’Agostino is a story of its own …
LINKS TO PREVIOUS ARTICLES ON WILSON AUDIO
Wilson Audio / David A. and Daryl Wilson